Method for removing iron and silicon impurities during regeneration of aluminum scraps
A technology of aluminum regeneration and impurity, applied in the direction of improving process efficiency, etc., can solve the problems of high energy consumption, unsuitable for industrial scale-up production requirements, etc., achieve the effect of simple process steps, meet the requirements of industrial large-scale production, and process requirements are not harsh
- Summary
- Abstract
- Description
- Claims
- Application Information
AI Technical Summary
Problems solved by technology
Method used
Examples
Embodiment 1
[0028] A) Preparation of iron removal flux, 30% of borax, 25% of manganese chloride, 10% of calcium chloride, 15% of calcium oxide, 5% of magnesium carbonate, 5% of sulfur and 10% of titanium dioxide weighed by mass % are put into A container with a stirrer, such as a stirred tank, is stirred for 2 minutes at a stirring speed of 240 rpm to obtain a flux for removing iron, which is ready for use;
[0029] B) To prepare silicon removal flux, put 30% of calcium sulfide, 40% of activated carbon, 10% of sulfur, 10% of calcium oxide and 10% of titanium dioxide weighed by mass into a stirring container with a stirring device such as a stirring tank Stir for 8 minutes under the condition that the rotating speed of the stirring device is 120rpm, and obtain the silicon-removing flux, which is ready for use;
[0030] C) Waste aluminum smelting, first put the waste aluminum into the smelting furnace and melt it into a waste aluminum melt (also called waste aluminum melt, the same below), an...
Embodiment 2
[0034] A) To prepare iron removal flux, put 20% of borax, 20% of manganese chloride, 15% of calcium chloride, 10% of calcium oxide, 10% of magnesium carbonate, 10% of sulfur and 15% of titanium dioxide weighed by mass % into A container with a stirrer, such as a stirred tank, is stirred for 8 minutes at a stirring speed of 60 rpm to obtain a deironing flux for use;
[0035] B) To prepare silicon removal flux, put 40% of calcium sulfide, 20% of activated carbon, 5% of sulfur, 15% of calcium oxide and 20% of titanium dioxide weighed by mass into a stirring container with a stirring device such as a stirring tank Stir for 15 minutes at the rotating speed of the stirring device at 60 rpm to obtain a silicon-removing flux for use;
[0036] C) Waste aluminum smelting, first put the waste aluminum into the smelting furnace and melt it into a waste aluminum melt (also called waste aluminum melt, the same below), and then add it to the waste aluminum melt while stirring the waste alumi...
Embodiment 3
[0039] A) Prepare iron removal flux, put 20% borax, 30% manganese chloride, 20% calcium chloride, 10% calcium oxide, 5% magnesium carbonate, 5% sulfur and 10% titanium dioxide weighed by mass % into A container with a stirrer, such as in a stirred tank, is stirred for 15 minutes at a stirring speed of 120 rpm to obtain a deironing flux for use;
[0040] B) Prepare silicon removal flux, put 45% of calcium sulfide, 25% of activated carbon, 5% of sulfur, 10% of calcium oxide and 15% of titanium dioxide weighed by mass into a stirring container with a stirring device such as a stirring tank Stir for 2 minutes at a rotating speed of the stirring device of 240 rpm to obtain a silicon-removing flux for use;
[0041] C) Waste aluminum smelting, first put the waste aluminum into the smelting furnace and melt it into a waste aluminum melt (also called waste aluminum melt, the same below), and then add it to the waste aluminum melt while stirring the waste aluminum melt The iron removal...
PUM
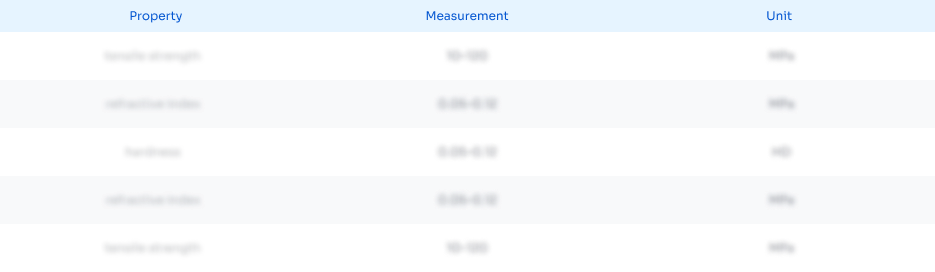
Abstract
Description
Claims
Application Information

- R&D
- Intellectual Property
- Life Sciences
- Materials
- Tech Scout
- Unparalleled Data Quality
- Higher Quality Content
- 60% Fewer Hallucinations
Browse by: Latest US Patents, China's latest patents, Technical Efficacy Thesaurus, Application Domain, Technology Topic, Popular Technical Reports.
© 2025 PatSnap. All rights reserved.Legal|Privacy policy|Modern Slavery Act Transparency Statement|Sitemap|About US| Contact US: help@patsnap.com