Cooling device during shrinkage fit process of shaft parts
A technology of cooling device and shaft parts, which is applied in the field of shaft parts assembly, can solve the problems of reducing production efficiency, affecting assembly accuracy, and jamming in the assembly process of hole parts, so as to reduce production gaps, improve production efficiency, and avoid precision. effect of the problem
- Summary
- Abstract
- Description
- Claims
- Application Information
AI Technical Summary
Problems solved by technology
Method used
Image
Examples
Embodiment approach
[0034] Such as figure 2As shown, this is a schematic diagram of the cooling water channel of the clamping arm. The cooling water coming in from the water inlet 5 enters the dense cooling water channel 7 that matches the shape of the clamping section (from the top view, if the clamping section is semicircular , then the dense cooling water channel 7 is a semi-circular ring whose radius is greater than that of the clamping section), where more cooling water can be collected to exchange heat with the clamping section, so as to achieve the purpose of rapidly cooling the assembly shaft; image 3 As shown, this is the schematic diagram b of the cooling water channel of the clamping arm. The cooling water coming in from the water inlet 5 enters the dense cooling water channel 7 of the clamping section. The dense cooling water channel 7 here is a snake perpendicular to the axial direction of the assembly axis. In order to achieve a better effect, this serpentine cooling channel match...
PUM
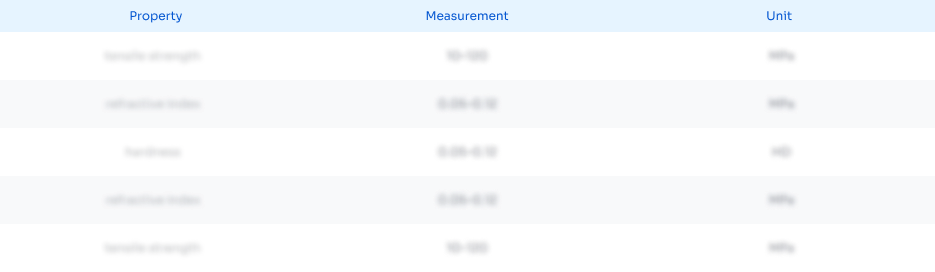
Abstract
Description
Claims
Application Information

- R&D
- Intellectual Property
- Life Sciences
- Materials
- Tech Scout
- Unparalleled Data Quality
- Higher Quality Content
- 60% Fewer Hallucinations
Browse by: Latest US Patents, China's latest patents, Technical Efficacy Thesaurus, Application Domain, Technology Topic, Popular Technical Reports.
© 2025 PatSnap. All rights reserved.Legal|Privacy policy|Modern Slavery Act Transparency Statement|Sitemap|About US| Contact US: help@patsnap.com