Preparation method of bononized lubricating oil dispersing agent
A technology of lubricating oil dispersant and boronation, which is applied in the field of preparation of boronated lubricating oil dispersant, to achieve the effects of good dispersion performance, good oxidation resistance and strong dispersing ability
- Summary
- Abstract
- Description
- Claims
- Application Information
AI Technical Summary
Problems solved by technology
Method used
Examples
Embodiment 1
[0026] (1) Synthesis of polyalkene-based succinic anhydride: add high-activity end-alkenyl polyisobutadiene and maleic anhydride in a three-neck flask with a molar ratio of 1:1, stir and heat up to a predetermined temperature, react for 6 hours, and use nitrogen Unreacted maleic anhydride was blown off to obtain polyalkenyl succinic anhydride.
[0027] (2) Add polyolefin-based succinic anhydride to a three-necked flask under nitrogen protection, heat up to 80°C, add 0.5 g of benzoyl peroxide as an initiator, stir well, add methacrylate, methacrylate and The molar ratio of polyolefin-based succinic anhydride is 1:1, the reaction is 6h, and the intermediate product A is separated;
[0028] (3) Add the intermediate product A and toluene with 10% mass of A in the three-necked flask, raise the temperature to 120°C under the protection of nitrogen, add tetraethylenepentamine, the molar ratio of A and tetraethylenepentamine is 1:1 and react for 5h, After the reaction, the solvent wa...
Embodiment 2
[0031] (1) Synthesis of polyalkene-based succinic anhydride: Add highly active terminal alkenyl polyisobutadiene and maleic anhydride in a three-neck flask with a molar ratio of 1:2, stir and heat up to the predetermined temperature, react for 8 hours, and use nitrogen Unreacted maleic anhydride was blown off to obtain polyalkenyl succinic anhydride.
[0032] (2) Add polyolefin-based succinic anhydride to a three-necked flask under nitrogen protection, heat up to 100°C, add 1 g of benzoyl peroxide as an initiator, stir evenly, add methacrylate, methacrylate and poly The molar ratio of alkenyl succinic anhydride is 5:1, react for 7h, and separate the intermediate product A;
[0033] (3) Add the intermediate product A and toluene with 15% mass of A in the three-necked flask, raise the temperature to 80°C under the protection of nitrogen, add tetraethylenepentamine, the molar ratio of A and tetraethylenepentamine is 1:1.5 and react for 8h, After the reaction, the solvent was rem...
Embodiment 3
[0036] (1) Synthesis of polyalkene-based succinic anhydride: add highly active terminal alkenyl polyisobutadiene and maleic anhydride in a three-neck flask with a molar ratio of 1:3, stir and heat up to a predetermined temperature, react for 7 hours, and use nitrogen Unreacted maleic anhydride was blown off to obtain polyalkenyl succinic anhydride.
[0037] (2) Add polyolefin-based succinic anhydride in a three-necked flask under nitrogen protection, heat up to 120°C, add 2 g of benzoyl peroxide as an initiator, stir evenly, add methacrylate, methacrylate and poly The molar ratio of alkenyl succinic anhydride is 10:1, react for 8h, and separate the intermediate product A;
[0038] (3) Add the intermediate product A and toluene with 30% mass of A in the three-necked flask, raise the temperature to 100°C under the protection of nitrogen, add tetraethylenepentamine, and react for 6 hours with the molar ratio of A and tetraethylenepentamine being 1:3, After the reaction, the solv...
PUM
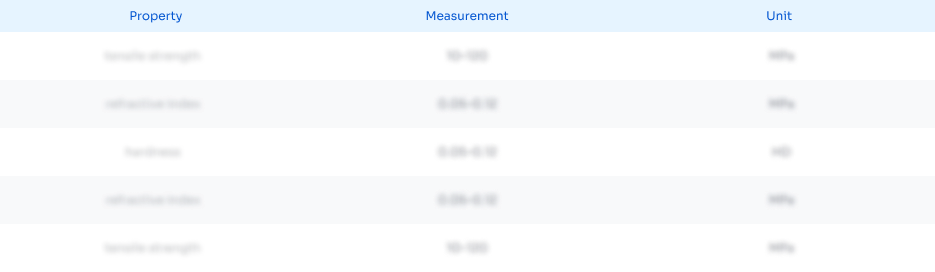
Abstract
Description
Claims
Application Information

- R&D
- Intellectual Property
- Life Sciences
- Materials
- Tech Scout
- Unparalleled Data Quality
- Higher Quality Content
- 60% Fewer Hallucinations
Browse by: Latest US Patents, China's latest patents, Technical Efficacy Thesaurus, Application Domain, Technology Topic, Popular Technical Reports.
© 2025 PatSnap. All rights reserved.Legal|Privacy policy|Modern Slavery Act Transparency Statement|Sitemap|About US| Contact US: help@patsnap.com