Speed reducer for planetary differential motion mechanical speed regulation
A technology of mechanical speed regulation and reducer, which is applied in the direction of clockwork mechanism, hoisting device, gear lubrication/cooling, etc. It can solve the problems of short service life of the motor, reduction of gear meshing accuracy, and inability to dissipate heat. Achieve the effects of prolonging service life, good lubrication, improving running stability and reliability
- Summary
- Abstract
- Description
- Claims
- Application Information
AI Technical Summary
Problems solved by technology
Method used
Image
Examples
Embodiment Construction
[0017] Such as figure 1 Shown: a reducer for planetary differential mechanical speed regulation, including a front cover 1, a box body 2, a vent cover 3, a rear end cover 4, a high-speed planetary part and a low-speed planetary part; the front end cover 1 and the rear end cover 4 pass through Bolts are fixed on the box body 2, and the vent cover 3 is located on the box body 2; the high-speed planetary part includes a high-speed gear shaft 5, a high-speed sun gear 6, and a high-speed planet carrier 7 set in the box body 2 and set on the high-speed gear shaft 5 , the high-speed planetary gear shaft 8 and the high-speed planetary gear 9 evenly distributed on the high-speed planetary carrier 7, and the high-speed internal gear 10 meshed with the high-speed planetary gear 9, and a bearing is arranged between the rear end cover 4 and the high-speed gear shaft 5 , the high-speed gear shaft 5 passes through the center of the bearing cover 11, and a rotary shaft lip seal ring is provid...
PUM
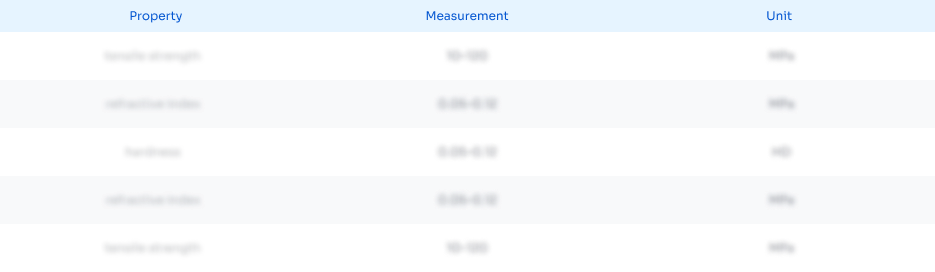
Abstract
Description
Claims
Application Information

- Generate Ideas
- Intellectual Property
- Life Sciences
- Materials
- Tech Scout
- Unparalleled Data Quality
- Higher Quality Content
- 60% Fewer Hallucinations
Browse by: Latest US Patents, China's latest patents, Technical Efficacy Thesaurus, Application Domain, Technology Topic, Popular Technical Reports.
© 2025 PatSnap. All rights reserved.Legal|Privacy policy|Modern Slavery Act Transparency Statement|Sitemap|About US| Contact US: help@patsnap.com