A flow distribution pair for a torque-balanced water hydraulic axial piston pump
An axial piston pump and torque balance technology, which is applied to the components of the pumping device for elastic fluid, pump control, pump components, etc., can solve the problems of poor lubricity, increased leakage flow, large leakage flow, etc. Achieve the effect of improving volumetric efficiency and service life, ensuring service life, and reducing friction and wear
- Summary
- Abstract
- Description
- Claims
- Application Information
AI Technical Summary
Problems solved by technology
Method used
Image
Examples
Embodiment Construction
[0021] The specific implementation manner will be further described below in conjunction with the accompanying drawings. Such as figure 1 , 2 , 3, the present invention mainly consists of a floating liner 1, a floating sleeve 2, a flow plate 3, the first, second, and third eddy current micro-displacement sensors 4, 5, 6, an amplification conditioning circuit 7, a control unit 8 and Composed of a power amplifier 9, the floating liner 1 is circular, made of magnetic stainless steel, with a stepped hole 1.1 in the center, and an annular flow distribution area 1.2 on the periphery of the stepped hole 1.1, which is evenly distributed along the circumference in the annular flow distribution area 1.2 7 or 9 flow distribution holes 1.3, one end of each floating sleeve 2 is installed in the flow distribution hole 1.3 corresponding to the floating liner 1, the periphery of the ring distribution area 1.2 is the ring displacement sensing area 1.4, and the periphery of the ring displaceme...
PUM
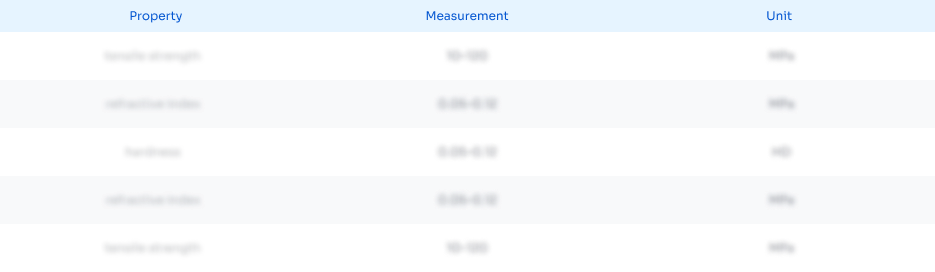
Abstract
Description
Claims
Application Information

- Generate Ideas
- Intellectual Property
- Life Sciences
- Materials
- Tech Scout
- Unparalleled Data Quality
- Higher Quality Content
- 60% Fewer Hallucinations
Browse by: Latest US Patents, China's latest patents, Technical Efficacy Thesaurus, Application Domain, Technology Topic, Popular Technical Reports.
© 2025 PatSnap. All rights reserved.Legal|Privacy policy|Modern Slavery Act Transparency Statement|Sitemap|About US| Contact US: help@patsnap.com