Low-temperature tempering method
A low-temperature, tempering oil technology, applied in the direction of quenching agent, heat treatment equipment, manufacturing tools, etc., can solve the problems of mismatch, tempering oil does not have the anti-rust performance of the workpiece, poor anti-rust performance, etc., to achieve easy cleaning, good thermal Oxidation stability, heat transfer, oil mist reduction effect
- Summary
- Abstract
- Description
- Claims
- Application Information
AI Technical Summary
Problems solved by technology
Method used
Image
Examples
Embodiment 1~10
[0022] Pump the base oil into the blending kettle, turn on the agitator and the heating switch, and when the oil is heated to 65°C, add the required amount of each component in turn, and continue to heat and stir at 65°C for 3 hours to obtain a uniform yellow liquid. There are a total of 100 parts of each component in the tempering oil composition, wherein each component and its content are shown in Table 1, and the corresponding performance index results are shown in Table 3 and Table 4.
[0023] In Table 1, T161A is high molecular weight succinimide, which was purchased from the Additive Factory of Jinzhou Petrochemical Company. T511 is 4,4-methylene bis(2,6-di-tert-butylphenol), Beijing Xingpu Fine Technology Development Company. T534 is alkylated diphenylamine, Beijing Xingpu Fine Technology Development Company. L-AN100, total loss system oil, Takahashi Refinery. L-AN150, total loss system oil, Takahashi Refinery. HVI650, lube base stock, Takahashi Refinery. HVI750, lu...
Embodiment 11
[0043] Under the condition of 150°C, the workpiece to be tempered was tempered in the tempering oil composition of [Example 3] for 3 hours. During use, it exhibits good thermal oxidation stability and heat transfer performance, and produces less sludge. The tempering oil composition can be used for 15 hours a day and can be used for one year. At the same time, after tempering, it has a short-term anti-rust effect on the workpiece, and no rust spots will appear for 40 days. It is easy to clean later, and the step of applying anti-rust oil is omitted, which saves production costs.
Embodiment 12
[0045] Under the condition of 200°C, the workpiece to be tempered was tempered in the tempering oil composition of [Example 8] for 2 hours. During use, it exhibits good thermal oxidation stability and heat transfer performance, and produces less sludge. The tempering oil composition can be used for 16 hours a day and can be used for one year. At the same time, after tempering, it has a short-term anti-rust effect on the workpiece, and no rust spots will appear for 30 days. It is easy to clean later, and the step of applying anti-rust oil is omitted, which saves production costs.
PUM
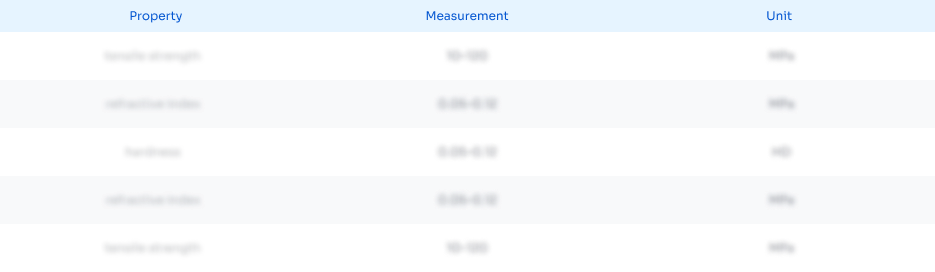
Abstract
Description
Claims
Application Information

- Generate Ideas
- Intellectual Property
- Life Sciences
- Materials
- Tech Scout
- Unparalleled Data Quality
- Higher Quality Content
- 60% Fewer Hallucinations
Browse by: Latest US Patents, China's latest patents, Technical Efficacy Thesaurus, Application Domain, Technology Topic, Popular Technical Reports.
© 2025 PatSnap. All rights reserved.Legal|Privacy policy|Modern Slavery Act Transparency Statement|Sitemap|About US| Contact US: help@patsnap.com