Special plastic composite additive and granulation processing method for PPR pipe
A technology of composite additives and pipes, which is applied in the field of production and the preparation of composite additives, can solve the problems of reduced additive effect, increased increase, poor breaking elongation, etc., to improve high and low temperature impact strength and high temperature water resistance Extraction performance, reduce the amount of additives, prolong the effect of breaking stretch
- Summary
- Abstract
- Description
- Claims
- Application Information
AI Technical Summary
Problems solved by technology
Method used
Image
Examples
Embodiment 1
[0008] Embodiment 1: A granulation processing method for making PPR pipes using the above-mentioned composite auxiliary agent, which is characterized in that it includes the following steps: first, 20% of antioxidant 330, 27% of antioxidant 168, 27% of antioxidant 1076, 8.5% of nucleating agent, 8.5% of acid remover, 5% of antistatic agent and 4% of chelating agent are put into the high-speed mixer according to the proportion and mixed, stirred for 45-60 seconds, and then the mixture is conveyed to the manufacturing plant through the screw feeder. The granulation operation is carried out in the granulator, the mixing temperature of the granulator is controlled to be less than 25°C, the temperature of the second stage is 55°C, the temperature of the machine head is 60°C, and the air cooling temperature is 25°C, and finally the cylindrical strip extruded by the granulator is The material is cooled by the air-cooling device of the conveyor belt. After the material is cooled, it pa...
Embodiment 2~8
[0009] Embodiment 2~8, with reference to embodiment 1, revise component mass percentage, make following table:
[0010]
[0011] Utilize the performance comparison of the PRR pipe produced by the composite additive of the present invention and the PRR pipe produced by the traditional additive:
[0012] 1. Comparison of melt index
[0013] Use the special plastic compound additive for PPR pipes of the present invention and traditional additives to compare the performance of PPR pipes:
[0014]
[0015] It can be seen from the above table that the special plastic compounding additive for PPR pipes of the present invention has the smallest change in melt index after multiple extrusions.
[0016] 2. Comparison of oxidation induction period
[0017] Use the special plastic compound additive for PPR pipes of the present invention and traditional additives to compare the performance of PPR pipes:
[0018]
[0019] It can be seen from the above table that the special plast...
PUM
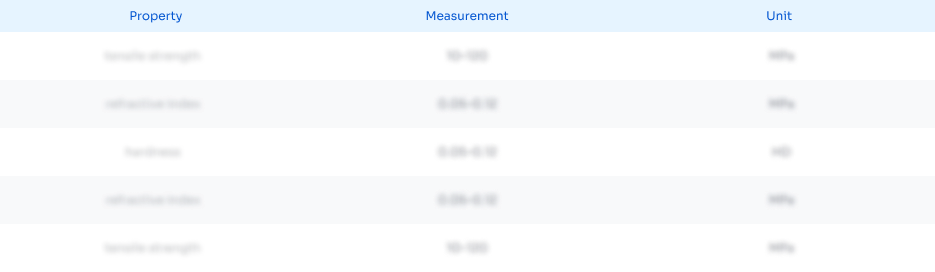
Abstract
Description
Claims
Application Information

- R&D
- Intellectual Property
- Life Sciences
- Materials
- Tech Scout
- Unparalleled Data Quality
- Higher Quality Content
- 60% Fewer Hallucinations
Browse by: Latest US Patents, China's latest patents, Technical Efficacy Thesaurus, Application Domain, Technology Topic, Popular Technical Reports.
© 2025 PatSnap. All rights reserved.Legal|Privacy policy|Modern Slavery Act Transparency Statement|Sitemap|About US| Contact US: help@patsnap.com