Method for preparing low carbon olefin through oxygenated chemicals
A compound and carbon olefin technology, which is applied in the field of producing low-carbon olefins from oxygen-containing compounds, can solve the problems of low yield of low-carbon olefins and the like, and achieve the effect of improving the yield
- Summary
- Abstract
- Description
- Claims
- Application Information
AI Technical Summary
Problems solved by technology
Method used
Image
Examples
Embodiment 1
[0020] in such as figure 1In the shown reaction device, methanol with a purity of 99.5% enters the first fluidized bed reaction zone and contacts with the SAPO-34 catalyst. In the fluidized bed reaction zone, the gas phase stream is separated from the catalyst and enters the separation section. The catalyst in the second fluidized bed reaction zone is divided into two parts. In terms of mass fraction, 40% returns to the first fluidized bed reaction zone, and 60% enters the lifting The tube regeneration zone is then lifted to the dense-phase bed regeneration zone to form a regenerated catalyst. The regenerated catalyst is divided into two parts, 20% of which is returned to the first fluidized bed reaction zone, and 80% is returned to the riser regeneration zone after heat extraction. The first fluidized bed reaction zone is a fast bed, and the reaction conditions in the first fluidized bed reaction zone are: the reaction temperature is 400°C, the reaction pressure is 0.01MPa in...
Embodiment 2
[0023] According to the conditions and steps described in Example 1, methanol with a purity of 99.5% enters the first fluidized bed reaction zone, contacts with the SAPO-34 catalyst, and the gas phase flow and catalyst generated are distributed through the top of the first fluidized bed reaction zone The plate enters the second fluidized bed reaction zone, and the gaseous phase stream is separated from the catalyst and enters the separation section. The catalyst in the second fluidized bed reaction zone is divided into two parts. In terms of mass fraction, 80% returns to the first fluidized bed reaction zone. 20% enters the riser regeneration zone, and then is lifted to the dense bed regeneration zone to form a regenerated catalyst. The regenerated catalyst is divided into two parts, 60% returns to the first fluidized bed reaction zone, and 40% returns to the riser for regeneration after heat extraction Area. The reaction conditions in the first fluidized bed reaction zone are...
Embodiment 3
[0026] According to the conditions and steps described in Example 2, the catalyst in the second fluidized bed reaction zone is divided into two parts, in terms of mass fraction, 50% returns to the first fluidized bed reaction zone, and 50% enters the riser regeneration zone, and then It is lifted to the dense-phase bed regeneration zone to form a regenerated catalyst. The regenerated catalyst is divided into two parts, 50% returns to the first fluidized bed reaction zone, and 50% returns to the riser regeneration zone after heat extraction. The reaction conditions in the first fluidized bed reaction zone are: the reaction temperature is 470°C, the reaction pressure is 0.01MPa in gauge pressure, and the gas phase velocity is 1.5 m / s; the reaction conditions in the second fluidized bed reaction zone are: the reaction temperature is 500°C, the reaction pressure is 0.01MPa in terms of gauge pressure, the gas phase velocity is 0.8 m / s, the average carbon deposition mass fraction of ...
PUM
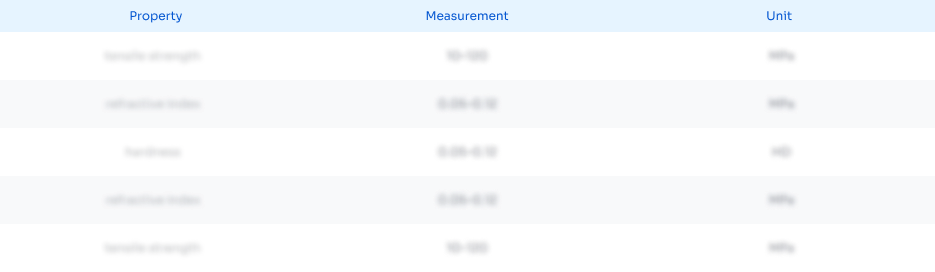
Abstract
Description
Claims
Application Information

- R&D
- Intellectual Property
- Life Sciences
- Materials
- Tech Scout
- Unparalleled Data Quality
- Higher Quality Content
- 60% Fewer Hallucinations
Browse by: Latest US Patents, China's latest patents, Technical Efficacy Thesaurus, Application Domain, Technology Topic, Popular Technical Reports.
© 2025 PatSnap. All rights reserved.Legal|Privacy policy|Modern Slavery Act Transparency Statement|Sitemap|About US| Contact US: help@patsnap.com