Water mist cooling method for normalizing treatment of large-scale casting and forging
A normalizing heat treatment and water mist cooling technology, applied in heat treatment furnaces, heat treatment equipment, furnace types, etc., can solve the problems of low atomization rate, large operation cost, large equipment investment, etc., and achieve the effect of uniform water volume and uniform cooling
- Summary
- Abstract
- Description
- Claims
- Application Information
AI Technical Summary
Problems solved by technology
Method used
Image
Examples
Embodiment Construction
[0014] The present invention will be described in detail below in conjunction with the accompanying drawings and specific embodiments.
[0015] refer to figure 1 , figure 2 , the present invention is a water mist cooling method for normalizing heat treatment of large castings and forgings. row), the inlet ports of multiple water inlet holes 10 of each atomizing nozzle 2 are connected to a water volume regulating valve 4, and the water volume regulating valve 4 of each horizontal row is connected with the cooling water pipe 3 of the horizontal row at the same time, and all cooling After the water pipe 3 merges, it is connected with the water outlet end of the water pipe main valve 7, and the water inlet end of the water pipe main valve 7 is connected with the cooling water source; the air inlet 9 of each atomizing nozzle 2 is provided with an air pressure regulating valve 5, and each horizontal row The air pressure regulating valve 5 is connected with the compressed air pipe...
PUM
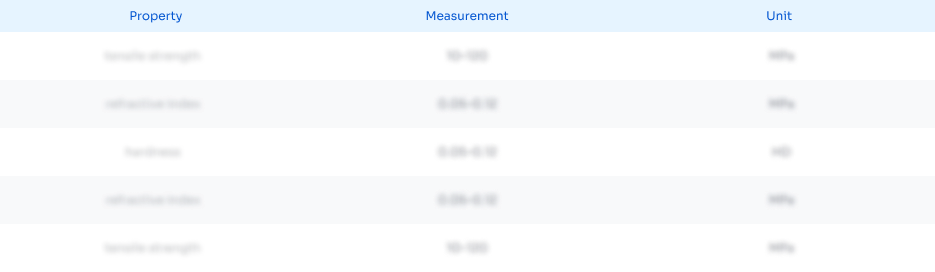
Abstract
Description
Claims
Application Information

- R&D Engineer
- R&D Manager
- IP Professional
- Industry Leading Data Capabilities
- Powerful AI technology
- Patent DNA Extraction
Browse by: Latest US Patents, China's latest patents, Technical Efficacy Thesaurus, Application Domain, Technology Topic, Popular Technical Reports.
© 2024 PatSnap. All rights reserved.Legal|Privacy policy|Modern Slavery Act Transparency Statement|Sitemap|About US| Contact US: help@patsnap.com