A method for removing environmental deposits in air film holes and narrow gaps of blades
A gas film hole and sediment technology, which is applied in the aerospace field, can solve the problems of small gas film hole diameter, damage to the base metal, block gas film cooling holes, etc., and achieve the effect of reducing the scrap rate.
- Summary
- Abstract
- Description
- Claims
- Application Information
AI Technical Summary
Problems solved by technology
Method used
Examples
Embodiment 1
[0009] Removal process of environmental deposits in air film holes and narrow gaps of cast nickel-based superalloy high-pressure turbine guide vanes:
[0010] (1) High temperature and high pressure lye removal
[0011] The parts that need to remove the sediment are stacked in the high-pressure reactor with the reaction part facing down without overlapping, and the working solution is 35% (mass concentration) potassium hydroxide solution, the working temperature is 180 ° C, and the working pressure is 4 Atmospheric pressure, the time is 180min. After the parts are taken out from the autoclave, they are washed repeatedly with hot water at 90°C to avoid residual lye.
[0012] (2) Potassium permanganate cleaning
[0013] Soak the parts in a potassium permanganate mixed solution (mass concentration: 10% potassium permanganate, 15% sodium hydroxide) for 60 minutes, the temperature of the solution is 70°C, put it into 90°C hot water immediately after being corroded by potassium perm...
Embodiment 2
[0018] Removal process of environmental deposits in air film holes and narrow gaps of nickel-based superalloy high-pressure turbine blades:
[0019] (1) High temperature and high pressure lye removal
[0020] The parts that need to remove the sediment are stacked in the high-pressure reactor with the reaction part facing down without overlapping. The working solution is 45% (mass concentration) potassium hydroxide solution, the working temperature is 200 ° C, and the working pressure is 4 Atmospheric pressure, the time is 300min. After the parts are taken out from the autoclave, they are washed with hot water at 90°C repeatedly to avoid residual lye.
[0021] (2) Potassium permanganate cleaning
[0022] Soak the parts in potassium permanganate mixed solution (mass concentration: 10% potassium permanganate, 20% sodium hydroxide) for 80min, the temperature of the solution is 90°C, put it into 90°C hot water immediately after being corroded by potassium permanganate Soak for 12...
Embodiment 3
[0027] Removal process of environmental deposits in air film holes and narrow gaps of cast nickel-based superalloy high-pressure turbine guide vanes:
[0028] (1) High temperature and high pressure lye removal
[0029] The parts that need to be removed from the sediment are stacked in the high-pressure reactor with the reaction part facing down without overlapping, and the working solution is 50% potassium hydroxide solution, the working temperature is 300 ° C, and the working pressure is 5 standard atmospheres. The time is 360min. After the parts are taken out from the autoclave, they are washed repeatedly with hot water at 90°C to avoid residual lye.
[0030] (2) Potassium permanganate cleaning
[0031] Soak the parts in potassium permanganate mixed solution (mass concentration: 15% potassium permanganate, 20% sodium hydroxide) for 100min, the temperature of the solution is 105°C, put it into 90°C hot water immediately after being corroded by potassium permanganate Soak fo...
PUM
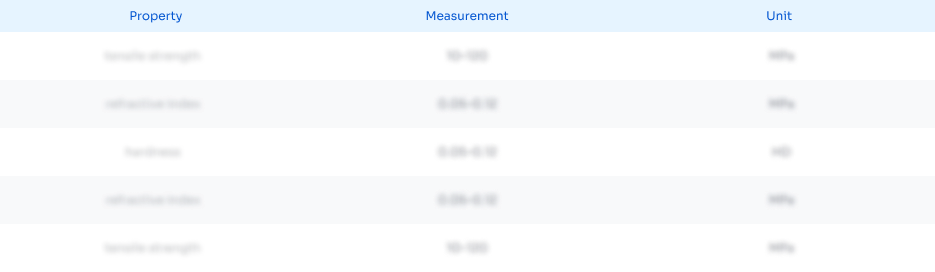
Abstract
Description
Claims
Application Information

- R&D Engineer
- R&D Manager
- IP Professional
- Industry Leading Data Capabilities
- Powerful AI technology
- Patent DNA Extraction
Browse by: Latest US Patents, China's latest patents, Technical Efficacy Thesaurus, Application Domain, Technology Topic, Popular Technical Reports.
© 2024 PatSnap. All rights reserved.Legal|Privacy policy|Modern Slavery Act Transparency Statement|Sitemap|About US| Contact US: help@patsnap.com