Split crystallizer for electroslag remelting of steel ingot with equal diameter
An electroslag remelting and crystallizer technology is applied in the field of electroslag remelting crystallizers, which can solve the problems of enlargement, uneven force on equipment, and uneven force, and achieves convenient use, stable process, and demoulding. Simple way to effect
- Summary
- Abstract
- Description
- Claims
- Application Information
AI Technical Summary
Problems solved by technology
Method used
Image
Examples
Embodiment 1
[0026] This embodiment relates to a split crystallizer for electroslag remelting of steel ingots with equal diameters, such as figure 1 As shown, it includes two symmetrically arranged first water-cooling jackets 1 and second water-cooling jackets 2 with semi-cylindrical cavities. The connected water inlet pipe 3 and the water outlet pipe 4 are provided with a positioning connection device 5 on one side of the two water cooling jackets, and a locking device 6 is also provided on the other side of the two water cooling jackets relative to the positioning connection device 5 .
[0027] The structure of the first water cooling jacket 1 is as follows: figure 2 As shown, a semi-cylindrical cavity is formed by a semicircular inner shell 8. The outer shell 9 surrounds the outside of the inner shell 8. The upper and lower end faces of the inner shell 8 and the outer shell 9 are connected together by a transverse connecting plate 10. The inner shell 8 The side end of the outer shell ...
Embodiment 2
[0034] This embodiment relates to a split crystallizer for equal-diameter electroslag remelting, which has roughly the same structure as the split crystallizer in Embodiment 1, except that the first water cooling jacket 1 in this embodiment structured as Figure 8 As shown, three first connecting lugs 54 with mounting shafts 55 are equidistantly arranged at the edge of one side thereof, and the mounting shafts 55 can pass through the connecting holes 52 on the connecting lugs 51 on the second water cooling jacket 2 , to achieve the same connection function as the connection pin 53, and the connection operation of the water cooling jacket is more convenient.
PUM
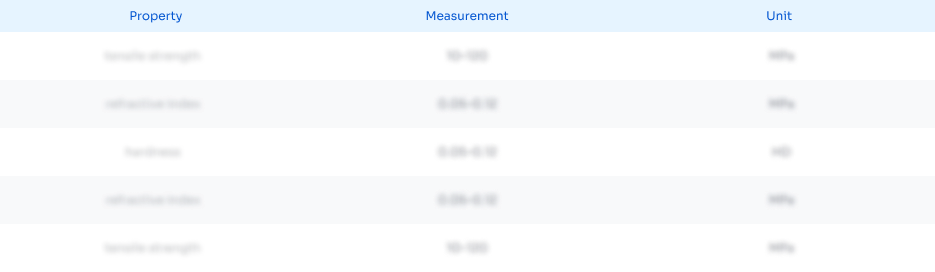
Abstract
Description
Claims
Application Information

- R&D Engineer
- R&D Manager
- IP Professional
- Industry Leading Data Capabilities
- Powerful AI technology
- Patent DNA Extraction
Browse by: Latest US Patents, China's latest patents, Technical Efficacy Thesaurus, Application Domain, Technology Topic, Popular Technical Reports.
© 2024 PatSnap. All rights reserved.Legal|Privacy policy|Modern Slavery Act Transparency Statement|Sitemap|About US| Contact US: help@patsnap.com