Production method of reconstituted tobacco leaves with clean, low consumption and high filling value
A technology for reconstituting tobacco leaves and a production method, which is applied in the directions of tobacco, tobacco preparation, application, etc., can solve the problems of poor sheet bulk, difficulty in backfilling, production cost, and high maintenance cost, so as to reduce energy consumption and water consumption, and avoid a large amount of loss. , the effect of improving production efficiency
- Summary
- Abstract
- Description
- Claims
- Application Information
AI Technical Summary
Problems solved by technology
Method used
Image
Examples
Embodiment 1
[0036] 1) After routine removal of impurities and drying, the tobacco powder is crushed into smoke powder of ≦80 mesh, and set aside;
[0037] 2) Soak the tobacco stems in hot water at 70°C at a mass ratio of 1:3, extract twice in continuous countercurrent, 40 minutes each time, and separate the solid and liquid to obtain the tobacco stem extract and residual tobacco stems;
[0038] 3) Add glycerin and calcium carbonate to the tobacco stem extract in step 2) according to the conventional amount of tobacco sheet production by the papermaking method, and mix evenly to obtain a modified tobacco stem extract;
[0039] 4) Take part of the modified tobacco stem extract in step 3), mix it with the tobacco powder in step 1) to a tobacco powder slurry with a mass concentration of 10%, and mix the rest of the modified tobacco stem extract in step 3) with step 2 ) after mixing the residual tobacco stems, beating to a coarse-stem pulp with a beating degree of 22°SR, and then finely beatin...
Embodiment 2
[0043] 1) After routine removal of impurities and drying, the shredded tobacco flakes and tobacco powder are crushed into smoke powder of ≦80 mesh for later use;
[0044] 2) Soak the tobacco stems in hot water at 45°C at a mass ratio of 1:6. First, use a conventional defibrillator to decompose the soaked tobacco stems into filaments, and then use continuous countercurrent extraction for 3 times, each time Extract for 20 minutes, and separate the solid and liquid to obtain tobacco stem extract and residual tobacco stem;
[0045] 3) Add propylene glycol, honey and calcium carbonate to the tobacco stem extract solution in step 2) according to the conventional amount of paper-making tobacco sheet production, and mix evenly to obtain a modified tobacco stem extract solution;
[0046] 4) Take part of the modified tobacco stem extract in step 3), mix it with the tobacco powder in step 1) to a tobacco powder slurry with a mass concentration of 20%, and mix the rest of the modified tob...
Embodiment 3
[0050] 1) After routine removal of impurities and drying of the broken tobacco flakes, the powder is crushed into smoke powder of ≦80 mesh and set aside;
[0051] 2) Soak the tobacco stems in hot water at 50°C at a mass ratio of 1:5, extract twice in a continuous countercurrent manner for 30 minutes each time, and separate the solid and liquid to obtain the tobacco stem extract and residual tobacco stems;
[0052] 3) Add sorbitol, honey, calcium carbonate, and pectinase to the tobacco stem extract solution in step 2) according to the conventional amount of paper-making tobacco sheet production, and mix evenly to obtain a modified tobacco stem extract solution;
[0053] 4) Take part of the modified tobacco stem extract in step 3), mix it with the tobacco powder in step 1) to a tobacco powder slurry with a mass concentration of 15%, and add conventional Wood pulp to wood fiber content is 5% mass ratio, beating to beating degree is the coarse wood pulp of 22 ° SR, then this coars...
PUM
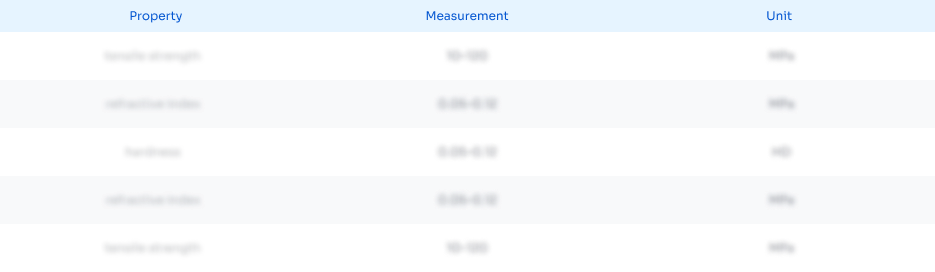
Abstract
Description
Claims
Application Information

- R&D Engineer
- R&D Manager
- IP Professional
- Industry Leading Data Capabilities
- Powerful AI technology
- Patent DNA Extraction
Browse by: Latest US Patents, China's latest patents, Technical Efficacy Thesaurus, Application Domain, Technology Topic, Popular Technical Reports.
© 2024 PatSnap. All rights reserved.Legal|Privacy policy|Modern Slavery Act Transparency Statement|Sitemap|About US| Contact US: help@patsnap.com