Automatic grease discharging structure of motor rolling bearing
A technology of rolling bearings and automatic discharge, which is applied in the direction of electric components, casings/covers/supports, electrical components, etc., can solve the problems of reducing motor efficiency, consuming electric energy, and high frictional heat generation between grease disc and grease, etc., to achieve Strengthen the convection heat dissipation capacity, ensure safe and reliable operation, and improve the effect of lubrication reliability
- Summary
- Abstract
- Description
- Claims
- Application Information
AI Technical Summary
Problems solved by technology
Method used
Image
Examples
Embodiment Construction
[0023] Depend on Figure 1-Figure 5 The automatic degreasing structure of the motor rolling bearing shown includes a rotating shaft 11, on which a bearing front cover 1, a bearing 13 and a bearing rear cover 12 are arranged in sequence from front to back, the bearing 13 is arranged in a bearing seat 14, and the bearing seat 14 is located between the bearing front cover 1 and the bearing rear cover 12. The bearing front cover 1 includes a radial cover plate 10 and a side plate arranged around the rear side of the outer edge of the cover plate 10. The rotating shaft 11 and the bearing front cover 1, the rotating shaft 11 and the The bearing back cover 12 is all plugged in, and a shaft penetration sealing structure is provided between the bearing front cover 1 and the rotating shaft 11. The bearing front cover 1, the bearing seat 14 and the bearing back cover 12 are fixedly connected by bolts. The bearing front cover 1, The connecting structure of the bearing block 14 and the bea...
PUM
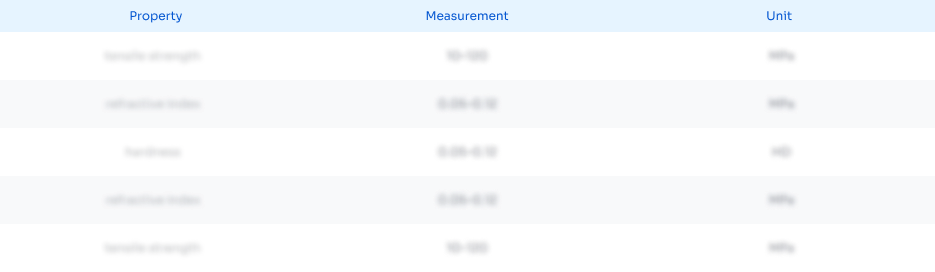
Abstract
Description
Claims
Application Information

- R&D Engineer
- R&D Manager
- IP Professional
- Industry Leading Data Capabilities
- Powerful AI technology
- Patent DNA Extraction
Browse by: Latest US Patents, China's latest patents, Technical Efficacy Thesaurus, Application Domain, Technology Topic, Popular Technical Reports.
© 2024 PatSnap. All rights reserved.Legal|Privacy policy|Modern Slavery Act Transparency Statement|Sitemap|About US| Contact US: help@patsnap.com