Medium-carbon steel large diesel engine output shaft hardening and tempering process
A diesel engine and output shaft technology, which is applied in the direction of manufacturing tools, furnace types, heat treatment equipment, etc., to avoid cracking and deformation out of tolerance, reduce the temperature difference between inside and outside, and increase the amount of solid solution
- Summary
- Abstract
- Description
- Claims
- Application Information
AI Technical Summary
Problems solved by technology
Method used
Image
Examples
Embodiment Construction
[0018] The present invention will be further described below in conjunction with drawings and embodiments.
[0019] The cross-sectional size of the output shaft of the large diesel engine in this embodiment is about 220mm, its mass is about 1000Kg, and its material is #45 forging. Such as figure 1 As shown, this embodiment includes the following steps:
[0020] (1) normalizing
[0021] Put the rough-processed large diesel engine output shaft into the trolley furnace at room temperature, raise the temperature in stages, keep it at 350±20°C and 600±20°C for 1 hour, and then raise the temperature to 870±20°C for 4-4.5 hours; After the heat preservation is completed, the output shaft of the large diesel engine is hoisted out, and cooled to room temperature with a fan.
[0022] (2) three quenching
[0023] The output shaft of the large diesel engine is put into the trolley furnace again at room temperature, and the temperature is raised in stages, and the temperature is kept at...
PUM
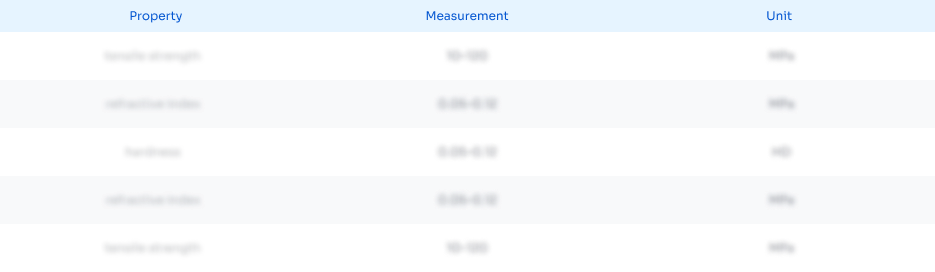
Abstract
Description
Claims
Application Information

- R&D
- Intellectual Property
- Life Sciences
- Materials
- Tech Scout
- Unparalleled Data Quality
- Higher Quality Content
- 60% Fewer Hallucinations
Browse by: Latest US Patents, China's latest patents, Technical Efficacy Thesaurus, Application Domain, Technology Topic, Popular Technical Reports.
© 2025 PatSnap. All rights reserved.Legal|Privacy policy|Modern Slavery Act Transparency Statement|Sitemap|About US| Contact US: help@patsnap.com