Method for producing industrial grade monoammonium phosphate through combination of wet process phosphoric acid and high-purity phosphoric acid
A technology of wet-process phosphoric acid and monoammonium phosphate, which is applied in the direction of phosphate, phosphorus oxyacid, etc., can solve the problems of unstable product quality and poor impurity removal effect, and solve the problems of difficult product quality assurance, short process route, The effect of good economic benefits
- Summary
- Abstract
- Description
- Claims
- Application Information
AI Technical Summary
Problems solved by technology
Method used
Image
Examples
Embodiment 1
[0040] (1) Put 1000kg of wet-process dilute phosphoric acid with a sulfate content of 2.5% into a desulfurization tank, heat to 75°C, add 26kg of mineral powder, stir for 60 minutes, put it into a centrifuge to separate the phosphogypsum, and transport the phosphogypsum To the phosphogypsum storage yard, the filtrate is desulfurized dilute phosphoric acid and put into the desulfurized phosphoric acid storage tank.
[0041] (2) Pump the desulfurized dilute phosphoric acid described in step 1 into a primary neutralization reaction tank, pass through gas ammonia to neutralize until the pH value reaches 4.0, put it into a centrifuge and filter it to obtain a primary neutralization filtrate, and put it into a primary neutralization reaction tank. Store the neutralized filtrate tank.
[0042] (3) Pump the primary neutralization filtrate in step 2 to the secondary neutralization reaction tank, add gas ammonia to neutralize the pH to 7.5, put it into a centrifuge to separate the secon...
Embodiment 2
[0049] (1) Put 1,500kg of wet-process dilute phosphoric acid with a sulfate content of 2.2% into a desulfurization tank, heat to 80°C, add 32.90kg of mineral powder, stir for 45 minutes, and put it into a centrifuge to separate the phosphogypsum and phosphogypsum Transported to the phosphogypsum yard, the filtrate is desulfurized dilute phosphoric acid and put into the desulfurized phosphoric acid storage tank.
[0050] (2) Pump the desulfurized dilute phosphoric acid described in step 1 into a primary neutralization reaction tank, pass through liquid ammonia to neutralize until the pH value reaches 4.5, put it into a centrifuge and filter it to obtain a primary neutralization filtrate, and put it into a primary neutralization reaction tank. Store the neutralized filtrate tank.
[0051] (3) Pump the primary neutralization filtrate in step 2 to the secondary neutralization reaction tank, add liquid ammonia to neutralize the pH to 8.0, put it into a centrifuge to separate the se...
Embodiment 3
[0057] (1) Put 1,300kg of wet-process dilute phosphoric acid with a sulfate content of 2.4% into a desulfurization tank, heat to 85°C, add 29.50kg of mineral powder, stir for 30 minutes, and put it into a centrifuge to separate the phosphogypsum and phosphogypsum Transported to the phosphogypsum yard, the filtrate is desulfurized dilute phosphoric acid and put into the desulfurized phosphoric acid storage tank.
[0058] (2) Pump the desulfurized dilute phosphoric acid described in step 1 into a primary neutralization reaction tank, pass through gas ammonia to neutralize until the pH value reaches 5.0, put it into a centrifuge and filter it to obtain a primary neutralization filtrate, and put it into a primary neutralization reaction tank. Store the neutralized filtrate tank.
[0059] (3) Pump the primary neutralization filtrate in step 2 to the secondary neutralization reaction tank, add liquid ammonia to neutralize the pH to 8.5, put it into a centrifuge to separate the secon...
PUM
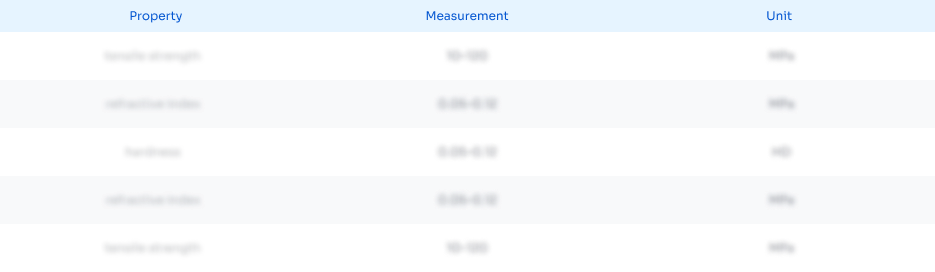
Abstract
Description
Claims
Application Information

- R&D
- Intellectual Property
- Life Sciences
- Materials
- Tech Scout
- Unparalleled Data Quality
- Higher Quality Content
- 60% Fewer Hallucinations
Browse by: Latest US Patents, China's latest patents, Technical Efficacy Thesaurus, Application Domain, Technology Topic, Popular Technical Reports.
© 2025 PatSnap. All rights reserved.Legal|Privacy policy|Modern Slavery Act Transparency Statement|Sitemap|About US| Contact US: help@patsnap.com