Method for manufacturing abrasion-resistant fastening piece through 3D printing technology
A 3D printing and 3D printer technology, which is applied in the electrical recording process using charge patterns, equipment using the electrical recording process with charge patterns, and electrical recording techniques. It can solve the problem of low wear resistance, waste, and durability of fasteners. Abrasion affects the service life of equipment and other issues
- Summary
- Abstract
- Description
- Claims
- Application Information
AI Technical Summary
Problems solved by technology
Method used
Examples
Embodiment 1
[0052] A method for manufacturing wear-resistant fasteners using 3D printing technology, the specific steps are:
[0053] (1) Build a 3D model of the internal workpiece in the computer. The 3D model is 0.5mm thicker than the outer layer of the entity, and then it is decomposed by the computer layer by layer to form a series of frontal plan views with serial numbers from top to bottom, and generate each frontal plan view. At the same time, a corresponding inverse plan is generated, that is, each layer gets the positive and negative graphics.
[0054] (2) Inject hot-melt powder into the 3D printer for printing or use a 3D printer with hot-melt powder to print.
[0055] (3) The positive and negative graphics generated by the computer are converted into light beams carrying positive and negative graphics information by the signal conversion device.
[0056] (4) Part of the photosensitive drum in the 3D printer is charged to obtain a potential, and scanned by the light beam carrying the po...
Embodiment 2
[0085] A method for manufacturing wear-resistant fasteners using 3D printing technology, the specific steps are:
[0086] (1) Build a 3D model of the internal workpiece in the computer. The 3D model is 0.5mm thicker than the outer layer of the entity, and then it is decomposed by the computer layer by layer to form a series of frontal plan views with serial numbers from top to bottom, and generate each frontal plan view. At the same time, a corresponding inverse plan is generated, that is, each layer gets the positive and negative graphics.
[0087] (2) Inject hot-melt powder into the 3D printer for printing or use a 3D printer with hot-melt powder to print.
[0088] (3) The positive and negative graphics generated by the computer are converted into light beams carrying positive and negative graphics information by the signal conversion device.
[0089] (4) Part of the photosensitive drum in the 3D printer is charged to obtain a potential, and scanned by the light beam carrying the po...
PUM
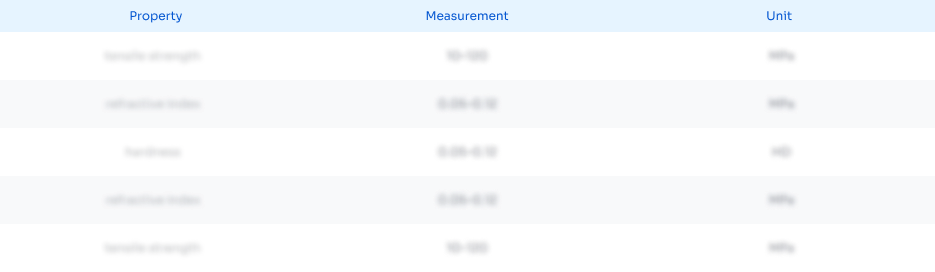
Abstract
Description
Claims
Application Information

- R&D
- Intellectual Property
- Life Sciences
- Materials
- Tech Scout
- Unparalleled Data Quality
- Higher Quality Content
- 60% Fewer Hallucinations
Browse by: Latest US Patents, China's latest patents, Technical Efficacy Thesaurus, Application Domain, Technology Topic, Popular Technical Reports.
© 2025 PatSnap. All rights reserved.Legal|Privacy policy|Modern Slavery Act Transparency Statement|Sitemap|About US| Contact US: help@patsnap.com