Spiral cut milling cutter with convex shoulder
A technology of spiral grooves and shoulders, which is applied in the direction of milling cutters, milling machine equipment, manufacturing tools, etc., can solve the problem of inconsistency in the width of the tool edge, and achieve the effect of consistent appearance quality, increased strength, and good cutting performance
- Summary
- Abstract
- Description
- Claims
- Application Information
AI Technical Summary
Problems solved by technology
Method used
Image
Examples
Embodiment Construction
[0013] The present invention will be further described below in conjunction with the examples, but not as a limitation of the present invention.
[0014] See figure 2 and image 3 , a spiral groove milling cutter with a shoulder, including a cutting part 1 for cutting work and a tool holder 2 for installation, the tooth shape of the cutting part 1 consists of a front edge face 11, a rear edge face 12, a tooth back 13 and a groove 15, a stepped shoulder 14 is provided at the joint between the rear edge surface 12 and the tooth back 13, and the height of the stepped shoulder 14 is h, so that there is a height difference between the rear edge surface 12 and the tooth back 13. The spiral groove milling cutter of processing band convex shoulder 14 is processed with special-purpose forming milling cutter, and groove and convex shoulder 14 are processed by one-shot molding during processing groove. Since there is a height difference h between the trailing edge surface 12 and the t...
PUM
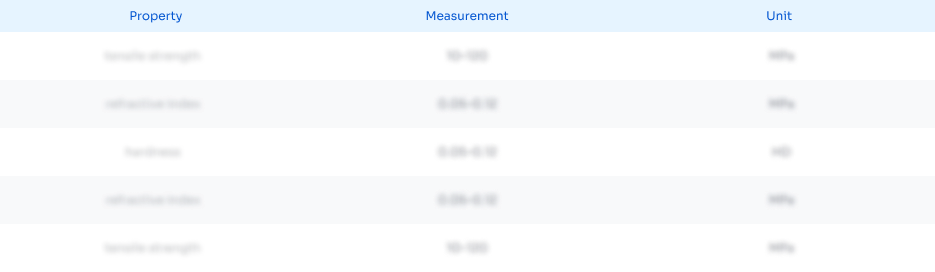
Abstract
Description
Claims
Application Information

- R&D Engineer
- R&D Manager
- IP Professional
- Industry Leading Data Capabilities
- Powerful AI technology
- Patent DNA Extraction
Browse by: Latest US Patents, China's latest patents, Technical Efficacy Thesaurus, Application Domain, Technology Topic, Popular Technical Reports.
© 2024 PatSnap. All rights reserved.Legal|Privacy policy|Modern Slavery Act Transparency Statement|Sitemap|About US| Contact US: help@patsnap.com