Precoated sand mixing process
A technology of coated sand and mixing, applied in manufacturing tools, metal processing equipment, casting and molding equipment, etc., can solve the problems of easy agglomeration, low irritating odor, low roughness, etc., to achieve deodorization performance and prevent The performance of the group is excellent, the irritating odor is small, and the effect of reducing the roughness
- Summary
- Abstract
- Description
- Claims
- Application Information
AI Technical Summary
Problems solved by technology
Method used
Examples
Embodiment 1
[0029] A coated sand mixing process, comprising the following steps
[0030] 1) Heat the raw sand, and when the temperature of the sand rises to 140~160°C, put the raw sand into the sand mixer, then add the adhesive to mix the sand and stir for 1~2min to obtain the adhesive sand, while stirring add deodorant;
[0031] 2) Add lubricant to the adhesive sand and mix the sand for 1~2min, cool down the adhesive sand after mixing, add curing agent and mix for 20~40s when the sand temperature of the adhesive sand drops to 105~110°C Obtain curing agent sand after;
[0032] 3) Add a lubricant to the curing agent sand and mix the sand for 1-2 minutes. After mixing, cool the curing agent sand, and when the sand temperature drops below 70°C, the sand will be produced to obtain coated sand;
[0033] The add-on of described bonding agent is 1.5% of former sand gross weight, and the add-on of described deodorant is 20% of bonding agent adding amount, and the adding amount of described curi...
Embodiment 2
[0035] Mixing step is with embodiment 1, and the difference with embodiment 1 is the proportioning of each composition, and difference is as follows:
[0036] The addition of the adhesive is 2% of the total weight of the original sand, the addition of the deodorant is 30% of the addition of the adhesive, and the addition of the curing agent is 15% of the addition of the adhesive. %, the add-on of the lubricant is 4% of the binder add-on, and the composition and weight ratio of the deodorant are: orange oil 60, turpentine oil 25, cedar oil 15, the composition and weight of the lubricant The proportion of parts is: zinc stearate 13, calcium stearate 87.
Embodiment 3
[0038] Mixing step is with embodiment 1, and the difference with embodiment 1 is the proportioning of each composition, and difference is as follows:
[0039] The addition of the adhesive is 2.5% of the total weight of the original sand, the addition of the deodorant is 40% of the addition of the adhesive, and the addition of the curing agent is 20% of the addition of the adhesive. %, the add-on of the lubricant is 6% of the binder add-on, the composition of the deodorant and its weight ratio are: orange oil 70, turpentine oil 20, cedar oil 10, the composition of the lubricant and its weight The proportion of parts is: zinc stearate 10, calcium stearate 90.
[0040] It can be seen that the coated sand produced by the coated sand mixing process of the present invention has the characteristics of small pungent odor, not easy to agglomerate, small roughness, and difficult to stick sand on castings.
PUM
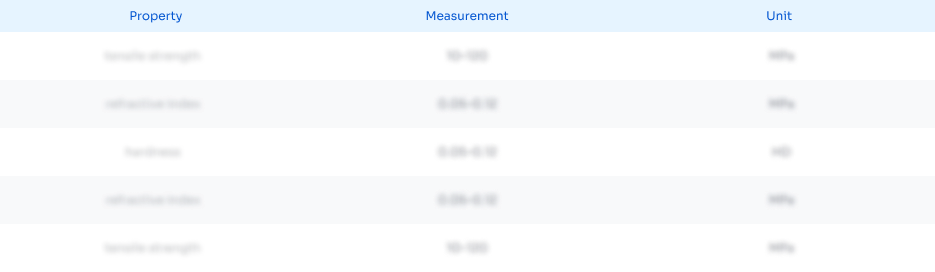
Abstract
Description
Claims
Application Information

- R&D
- Intellectual Property
- Life Sciences
- Materials
- Tech Scout
- Unparalleled Data Quality
- Higher Quality Content
- 60% Fewer Hallucinations
Browse by: Latest US Patents, China's latest patents, Technical Efficacy Thesaurus, Application Domain, Technology Topic, Popular Technical Reports.
© 2025 PatSnap. All rights reserved.Legal|Privacy policy|Modern Slavery Act Transparency Statement|Sitemap|About US| Contact US: help@patsnap.com