Biphenol compound preparation method
A biphenol and compound technology, applied in the field of preparation without using any solvent, can solve the problem of unsatisfactory effective conversion rate of raw materials, etc.
- Summary
- Abstract
- Description
- Claims
- Application Information
AI Technical Summary
Problems solved by technology
Method used
Image
Examples
Embodiment 1
[0022] Add 100g of 2,6-dimethylphenol into the reactor, and raise the temperature to 50°C under the protection of nitrogen. After fully melting the 2,6-dimethylphenol, add 1g of catalyst sodium hydroxide, and continue to heat up to 150°C, fully stir and mix evenly. Then stop feeding nitrogen, change to feed oxygen at a speed of 15ml / min, control the reaction temperature at 150~160°C, react for 6 hours, and the total oxygen feeding amount is 0.241mol (29.4% of the molar weight of raw materials). Stop feeding oxygen, change to nitrogen, and raise the temperature to 225~235°C to react for 2 hours. After the reaction, distill under reduced pressure of relative vacuum -0.07Mpa, collect 14g of 2,6-dimethylphenol fraction, wash and dry the crude product, and obtain the product 2,2',6,6'-tetramethyl -4,4'-biphenyldiphenol 85g white crystal, melting point 223~225℃, content 98.64%.
Embodiment 2
[0024] Add 100g of 2,6-di-tert-butylphenol into the reactor, raise the temperature to 45°C under nitrogen protection, melt the 2,6-di-tert-butylphenol, add 1.5g of catalyst calcium hydroxide, and continue to Raise the temperature to 160°C and stir well to mix evenly. Then stop feeding nitrogen, change to feed oxygen at a rate of 6.5ml / min, control the reaction temperature at 160~170°C, and react for 7 hours. . Stop feeding oxygen, change to nitrogen, heat up to 170-180°C and react for 2.6 hours. After the reaction, distill under reduced pressure at a relative vacuum of -0.08Mpa, collect 10g of 2,6-di-tert-butylphenol fraction, wash and dry the crude product to obtain the product 2,2',6,6'-tetra 89.5g of tert-butyl-4,4'-diphenol white crystals, melting point 185-187°C (standard product melting point 185-186°C), content 99.12%.
[0025] Infrared detection data of product structure: 1477.54 cm -1 , 1424.49 cm -1 (Stretching vibration of C=C benzene ring), 873.79 cm -1 (out-...
Embodiment 3
[0027] Add 100g of 2,6-di-tert-butylphenol into the reactor, raise the temperature to 45°C under nitrogen protection, melt the 2,6-di-tert-butylphenol, add 0.5g of sodium phenate catalyst, and continue to raise the temperature under nitrogen atmosphere Stir well to 170°C and mix well. Then stop feeding nitrogen, feed oxygen at a rate of 9.5ml / min, control the reaction temperature at 160-170°C, react for 5 hours, and the total oxygen feeding amount is 0.127mol (26.2% of the molar weight of raw materials). Stop feeding oxygen, change to nitrogen, and raise the temperature to 170-180°C for 3 hours. After the reaction, distill under reduced pressure at a relative vacuum of -0.09Mpa, collect 9g of 2,6-di-tert-butylphenol fraction, wash and dry the crude product to obtain the product 2,2',6,6'-tetra-tert Butyl-4,4'-diphenol white crystal 90g, melting point 185~187℃, content 99.08%.
PUM
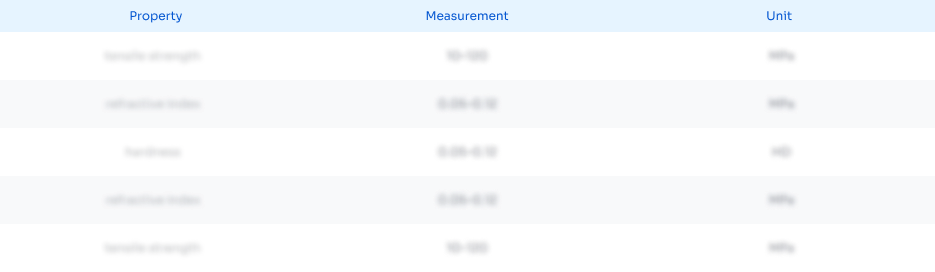
Abstract
Description
Claims
Application Information

- R&D
- Intellectual Property
- Life Sciences
- Materials
- Tech Scout
- Unparalleled Data Quality
- Higher Quality Content
- 60% Fewer Hallucinations
Browse by: Latest US Patents, China's latest patents, Technical Efficacy Thesaurus, Application Domain, Technology Topic, Popular Technical Reports.
© 2025 PatSnap. All rights reserved.Legal|Privacy policy|Modern Slavery Act Transparency Statement|Sitemap|About US| Contact US: help@patsnap.com