Process for preparing emulsion explosive by on-site upward deep hole filling
A technology of emulsion explosives and process methods, which is applied to explosives processing equipment, explosives, offensive equipment, etc., can solve the problems of drug waste, poor blasting effect, and high cost, and achieve the effects of cost reduction, resource saving, and no drug waste
- Summary
- Abstract
- Description
- Claims
- Application Information
AI Technical Summary
Problems solved by technology
Method used
Image
Examples
Embodiment 1
[0024] A process method for preparing emulsion explosives by filling deep holes upwards on site, comprising the following process steps:
[0025] (1) Preparation of emulsion
[0026] a. Water phase: mix sodium nitrate and ammonium nitrate in a ratio of 1:4 by weight, add water, mix evenly at 107.2°C, and adjust the pH value to 6 with concentrated ammonia water;
[0027] b. Oil phase: Mix maleic anhydride / styrene copolymer with dodecyl alcohol and n-decyl alcohol in a ratio of 7:1:1 by weight, and stir and react at 60°C for 2 hours to obtain reactant A, Then take 150g of reactant A, add 49g of neutral oil and 1g of diethylethanolamine to reactant A, heat to 90°C-100°C and continue the reaction for 4h to obtain an oil phase;
[0028] c. Mixing and emulsification of the water phase and the oil phase: heat the above water phase to 107.2°C, then add it into the oil phase at a rate of 200g per 3min, and stir under low shear conditions until a low-viscosity emulsion is formed, and t...
Embodiment 2
[0032] A process method for preparing emulsion explosives by filling deep holes upwards on site, comprising the following process steps:
[0033] (1) Preparation of emulsion
[0034] a. Water phase: mix sodium nitrate and ammonium nitrate in a ratio of 1:8 by weight, add water, and mix evenly at 104.4°C, adjust the pH value to 4 with concentrated ammonia water;
[0035] b. Oil phase: Mix maleic anhydride / styrene copolymer with dodecanol and n-decyl alcohol in a ratio of 8:1:1 by weight, and stir and react at 70°C for 2 hours to obtain reactant A, Then take 150g of reactant A, add 49g of neutral oil and 1g of diethylethanolamine to reactant A, heat to 90°C-100°C and continue the reaction for 4h to obtain an oil phase;
[0036] c. Mixing and emulsification of the water phase and the oil phase: heat the above water phase to 104.4°C, then add it into the oil phase at a rate of 200g per 4min, and stir under low shear conditions until a low-viscosity emulsion is formed. The emulsi...
Embodiment 3
[0039] Embodiment 3: A kind of process method of carrying out deep hole filling on the spot to prepare emulsion explosive, consists of the following process steps:
[0040] (1) Preparation of emulsion
[0041] a. Water phase: mix sodium nitrate and ammonium nitrate in a ratio of 1:6 by weight, add water, mix evenly at 105°C, and adjust the pH value to 5 with concentrated ammonia water;
[0042] b. Oil phase: Mix maleic anhydride / styrene copolymer with dodecanol and n-decyl alcohol in a ratio of 7.5:1:1 by weight, and stir and react at 60°C-70°C for 2h to obtain the reaction Material A, and then take 150g of reactant A, and add 49g of neutral oil and 1g of diethylethanolamine to reactant A, heat to 90°C-100°C and continue the reaction for 4h to obtain an oil phase;
[0043] c. Mixing and emulsification of the water phase and the oil phase: heat the above water phase to 106°C, then add 200g to the oil phase at a rate of 3-4min, and stir under low shear conditions until a low-vi...
PUM
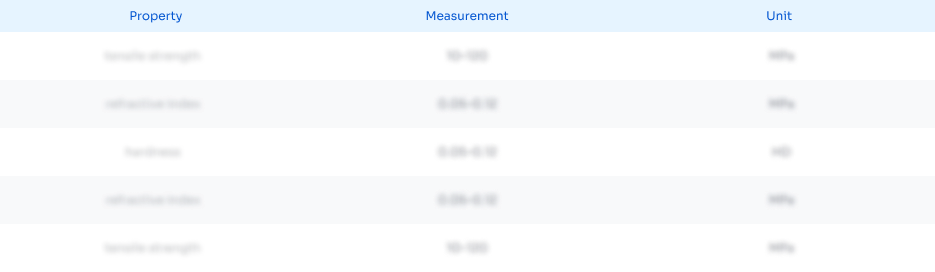
Abstract
Description
Claims
Application Information

- R&D Engineer
- R&D Manager
- IP Professional
- Industry Leading Data Capabilities
- Powerful AI technology
- Patent DNA Extraction
Browse by: Latest US Patents, China's latest patents, Technical Efficacy Thesaurus, Application Domain, Technology Topic, Popular Technical Reports.
© 2024 PatSnap. All rights reserved.Legal|Privacy policy|Modern Slavery Act Transparency Statement|Sitemap|About US| Contact US: help@patsnap.com