Composite material roller and preparation method thereof
A technology of composite material and composite material layer, which is applied in the field of composite material roller and its preparation, can solve the problems that the wear-resistant rubber layer is easy to partially fall off, the corrosion resistance of the roller is reduced, and the metal roller is exposed outside, so as to avoid slipping and reduce Effect of Mass and Rotational Dynamics, Increasing Friction
- Summary
- Abstract
- Description
- Claims
- Application Information
AI Technical Summary
Problems solved by technology
Method used
Image
Examples
Embodiment 1
[0037]In the first step, take 100 kg of lactam monomer, heat and melt it, dehydrate it, add 0.09 kg of sodium hydroxide and continue dehydration for 33 minutes;
[0038] In the second step, add 18 kg of ultra-high molecular polyethylene, 0.04 kg of xylene and 0.9 kg of maleic anhydride monomer, and stir for 17 minutes to fully mix the ultra-high molecular polyethylene in the caprolactam monomer melt until uniformly dispersed;
[0039] In the third step, under the condition of a high temperature of 190 degrees Celsius, continue to add 0.18 kg of soda, 1.4 kg of hexaphosphine and 0.18 kg of wear-resistant oil and stir for 11 minutes;
[0040] In the fourth step, the temperature is lowered to 155 degrees centigrade, and 0.09 kg of graphite, 0.04 kg of antimony trioxide, and 0.28 kg of carbon black are added, and stirred for 14 minutes;
[0041] In the fifth step, 0.18 kg of molybdenum disulfide and 0.18 kg of graphite are finally added, mixed quickly and evenly, and then die-cast...
Embodiment 2
[0043] In the first step, take 100 kg of lactam monomer, heat it to melt, dehydrate it, add 0.11 kg of sodium hydroxide and continue dehydration for 25 minutes;
[0044] In the second step, add 22 kg of ultra-high molecular polyethylene, 0.06 kg of xylene and 1.1 kg of maleic anhydride monomer, and stir for 13 minutes to fully mix the ultra-high molecular polyethylene in the caprolactam monomer melt until uniformly dispersed;
[0045] The 3rd step, under the condition of high temperature 170 degrees centigrade, continue to add 0.22 kilogram of sulfuric acid, 1.6 kilogram of hexaphosphine and 0.22 kilogram of wear-resistant oil and stir for 10 minutes;
[0046] In the fourth step, lower the temperature to 145 degrees Celsius, add 0.11 kg of Sanhe turquoise, 0.06 kg of magnesium hydroxide, and 0.32 kg of carbon black, and stir for 16 minutes;
[0047] In the fifth step, 0.22 kg of molybdenum disulfide and 0.22 kg of graphite are finally added, mixed quickly and evenly, and then ...
Embodiment 3
[0049] In the first step, take 100 kg of lactam monomer, heat and melt it, dehydrate it, add 0.095 kg of sodium hydroxide and continue dehydration for 29 minutes;
[0050] In the second step, add 19 kg of ultra-high molecular polyethylene, 0.045 kg of xylene and 0.95 kg of maleic anhydride monomer, and stir for 14 minutes to fully mix the ultra-high molecular polyethylene in the caprolactam monomer melt until uniformly dispersed;
[0051] In the third step, under the condition of a high temperature of 175 degrees Celsius, continue to add 0.19 kilograms of soda, 1.45 kilograms of hexaphosphine and 0.19 kilograms of wear-resistant oil and stir for 10 minutes;
[0052] In the fourth step, the temperature was lowered to 146 degrees Celsius, and 0.095 kg of graphite, 0.045 kg of antimony trioxide, and 0.29 kg of carbon black were added, and stirred for 14 minutes;
[0053] In the fifth step, 0.19 kg of molybdenum disulfide and 0.19 kg of graphite are finally added, mixed quickly an...
PUM
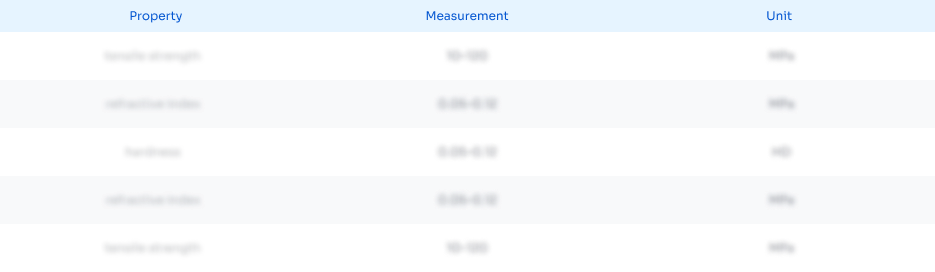
Abstract
Description
Claims
Application Information

- Generate Ideas
- Intellectual Property
- Life Sciences
- Materials
- Tech Scout
- Unparalleled Data Quality
- Higher Quality Content
- 60% Fewer Hallucinations
Browse by: Latest US Patents, China's latest patents, Technical Efficacy Thesaurus, Application Domain, Technology Topic, Popular Technical Reports.
© 2025 PatSnap. All rights reserved.Legal|Privacy policy|Modern Slavery Act Transparency Statement|Sitemap|About US| Contact US: help@patsnap.com