Beneficiation method for comprehensively reclaiming complex multi-metal micro-grain cassiterite sulphide ore
A technology for a stone sulfide ore and a beneficiation method, which is applied in the field of beneficiation of complex polymetallic fine-grained cassiterite sulfide ore, can solve the problems of unfavorable automatic control, low recovery rate, low raw ore grade, etc. Automatically control and improve the effect of flotation index
Active Publication Date: 2014-02-05
CINF ENG CO LTD
View PDF5 Cites 11 Cited by
- Summary
- Abstract
- Description
- Claims
- Application Information
AI Technical Summary
Problems solved by technology
[0003] The separation of tin ore mainly adopts different methods according to its different properties: the recovery of coarse cassiterite mainly adopts the gravity separation (shaking table, dense medium mineral processing) process, which is simple, low in cost and less polluting to the environment However, with the increase of mining efforts in recent years, my country's tin ore resources have gradually shown the characteristics of low ore grade, fine particle size and complex
Method used
the structure of the environmentally friendly knitted fabric provided by the present invention; figure 2 Flow chart of the yarn wrapping machine for environmentally friendly knitted fabrics and storage devices; image 3 Is the parameter map of the yarn covering machine
View moreImage
Smart Image Click on the blue labels to locate them in the text.
Smart ImageViewing Examples
Examples
Experimental program
Comparison scheme
Effect test
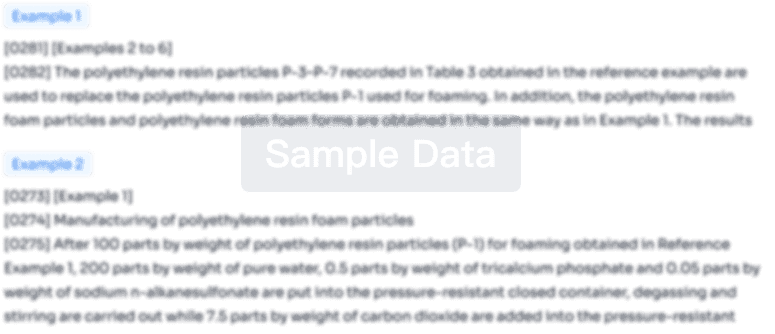
PUM
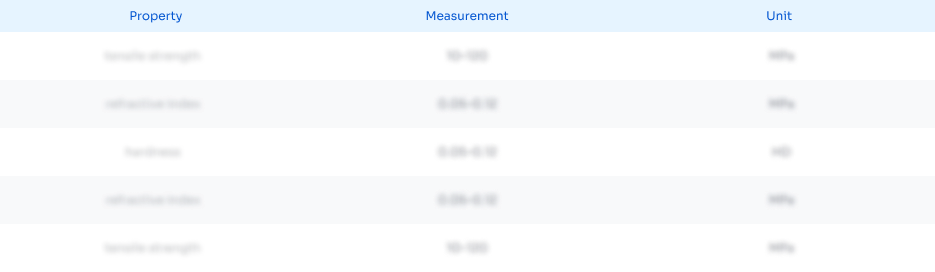
Abstract
The invention relates to a beneficiation method for comprehensively reclaiming complex multimetal micro-grain cassiterite sulphide ore by adopting a magnetic separation-flotation combined technology. According to the dissemination characteristics of the ore, more than 95% of the ore is ground to be -200 mesh at first, and then magnetic mineral in the ore is removed through high-gradient magnetic separation; according to the flotability difference of the mineral, sulphide ore flotation is performed on the magnetic separation tailings, and follow-up beneficiation is performed on the flotation concentrate to obtain copper and zinc concentrate reaching the sale standard; cassiterite flotation is performed on the flotation tailings, and through the adoption of a combined restrainer (sodium carboxymethyl cellulose and sodium silicate) and a hydroximic acid-type collector, and control over the flotation temperature and the reagent action time in the flotation process, tin concentrate of which the grade and recovery rate are higher than 40% can be obtained. Through the adoption of the technological process, the consumption of flotation reagents (especially tin flotation reagent) is lowered greatly; cassiterite flotation and sulphide ore flotation are separated, so that the stability of the flotation results can be ensured, and the achievement of automatic control over the process is facilitated; all metal is utilized comprehensively, which conforms to the national condition of resource shortage in our country.
Description
technical field [0001] The invention belongs to the field of polymetallic ore beneficiation, and in particular relates to a method for beneficiating complex polymetallic fine-grained cassiterite sulfide ore. Background technique [0002] There are two main forms of cassiterite in fine-grained cassiterite sulfide ore: one is the sulfide-type cassiterite in "green rock", with a particle size of 0.005mm-0.037mm; the other is vein-like and veinlet-like Lithophile-like cassiterite, mainly associated with mica-quartz schist, with a particle size of 0.017mm-0.1mm. In addition, such ores are often associated with chalcopyrite (0.015mm-0.1mm in particle size), sphalerite (0.02mm-0.1mm in particle size), arsenopyrite, pyrrhotite, etc. [0003] The separation of tin ore mainly adopts different methods according to its different properties: the recovery of coarse cassiterite mainly adopts the gravity separation (shaking table, dense medium mineral processing) process, which is simple, ...
Claims
the structure of the environmentally friendly knitted fabric provided by the present invention; figure 2 Flow chart of the yarn wrapping machine for environmentally friendly knitted fabrics and storage devices; image 3 Is the parameter map of the yarn covering machine
Login to View More Application Information
Patent Timeline

IPC IPC(8): B03B7/00B03D1/00
Inventor 柯丽芳吉红
Owner CINF ENG CO LTD
Features
- Generate Ideas
- Intellectual Property
- Life Sciences
- Materials
- Tech Scout
Why Patsnap Eureka
- Unparalleled Data Quality
- Higher Quality Content
- 60% Fewer Hallucinations
Social media
Patsnap Eureka Blog
Learn More Browse by: Latest US Patents, China's latest patents, Technical Efficacy Thesaurus, Application Domain, Technology Topic, Popular Technical Reports.
© 2025 PatSnap. All rights reserved.Legal|Privacy policy|Modern Slavery Act Transparency Statement|Sitemap|About US| Contact US: help@patsnap.com