Production method of vortex spun colored hollow yarns
A vortex spinning and colored technology, which is applied in yarn, textile and paper making, etc., can solve the problems of restricting product development and development, high temperature and humidity environment, affecting processing, etc., and achieve the effect of improving hand feeling, increasing application range and improving comfort
- Summary
- Abstract
- Description
- Claims
- Application Information
AI Technical Summary
Problems solved by technology
Method used
Image
Examples
Embodiment 1
[0019] The preparation method of the vortex spinning colored hollow yarn in this embodiment comprises four steps of raw sliver preparation, pre-drawing, drawing and vortex spinning, and the specific steps are as follows:
[0020] (1) Raw sliver preparation: put the colored viscose fiber and natural color vinylon into the cotton mixing device for mechanical mixing, and make viscose fiber raw sliver and vinylon raw sliver of equal gram weight.
[0021] Among them, the mechanical mixing treatment refers to the opening process. Specifically, the viscose fiber is opened for the first time or called pre-opening. The pre-opening is carried out in the cotton mixing device. For the structure of the cotton mixing device, see Figure 1 and figure 2 , the beater speed of the cotton mixing device is controlled at 740r / min, and then the second opening or deep opening is performed in the cotton opener (model FA006), and the beater speed of the cotton opener is controlled at 450r / min; Vinylon ...
Embodiment 2
[0027] The working principle and process of this embodiment are the same as those in Embodiment 1, the difference being:
[0028](1) Raw sliver preparation: in the pre-opening of viscose fiber, the beater speed of the cotton mixing device is controlled at 650r / min; in the deep opening, the beater speed of the cotton opener is controlled at 460r / min; The beating speed of the cotton machine is controlled at 460r / min, and the vinylon and viscose fibers are sent to the carding machine after being loosened. Roll speed 940 rpm, delivery speed 100 m / min, cylinder-flat gauge 10 / 8.8 / 8.5 / 8.5, rear pre-opening gauge 18 / 17 / 16 / 16, front fixed carding The gauge is 10, the gap between the entrance and the outlet of the large drain bottom is 3 mm, and the exit is 0.8 mm, forming viscose fiber raw sliver and vinylon raw sliver respectively.
[0029] (2) Pre-drawing: The natural color vinylon raw sliver and viscose fiber raw sliver are drawn twice to obtain vinylon sliver and viscose fiber sli...
Embodiment 3
[0033] The working principle and process of this embodiment are the same as those in Embodiment 1, the difference being:
[0034] (1) Raw sliver preparation: in the pre-opening of viscose fiber, the beater speed of the cotton mixing device is controlled at 850r / min; in the deep opening, the beater speed of the cotton opener is controlled at 380r / min; The beating speed of the cotton machine is controlled at 380r / min, and the vinylon and viscose fibers are sent to the carding machine after opening. In the carding machine, the carding speed is controlled at 140m / min, the cylinder speed is 450 rpm, Roll speed 1160 rpm, delivery speed 80m / min, cylinder-flat gauge 10 / 9 / 8.8 / 8.8, rear pre-carding gauge 18 / 16 / 16 / 16, front fixed carding gauge The gap is 14, the gap between the entrance and the outlet is 0.4mm, and the gap between the bottom and the bottom is 5mm, forming viscose fiber raw sliver and vinylon raw sliver respectively.
[0035] (2) Pre-drawing: The natural color vinylon ra...
PUM
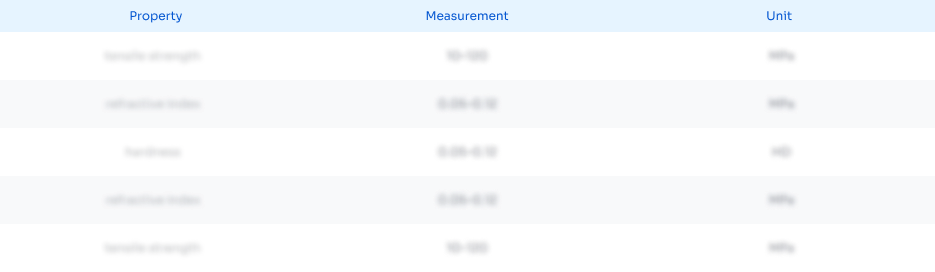
Abstract
Description
Claims
Application Information

- R&D Engineer
- R&D Manager
- IP Professional
- Industry Leading Data Capabilities
- Powerful AI technology
- Patent DNA Extraction
Browse by: Latest US Patents, China's latest patents, Technical Efficacy Thesaurus, Application Domain, Technology Topic, Popular Technical Reports.
© 2024 PatSnap. All rights reserved.Legal|Privacy policy|Modern Slavery Act Transparency Statement|Sitemap|About US| Contact US: help@patsnap.com