sliding nozzle
A sliding, nozzle technology, used in engine components, combustion engines, machines/engines, etc., can solve the problems of scrapped nozzle ring components, low assembly accuracy, large positioning errors, etc., to eliminate material deformation and process accuracy loss, improve Transmission accuracy and wear resistance, effect of quantity reduction and fit accuracy
- Summary
- Abstract
- Description
- Claims
- Application Information
AI Technical Summary
Problems solved by technology
Method used
Image
Examples
Embodiment Construction
[0030] The following will clearly and completely describe the technical solutions in the embodiments of the present invention. Obviously, the described embodiments are only some of the embodiments of the present invention, rather than all the embodiments. Based on the embodiments of the present invention, all other embodiments obtained by persons of ordinary skill in the art without making creative efforts belong to the protection scope of the present invention.
[0031] see Figure 2-Figure 6 , the embodiment of the present invention includes:
[0032] A sliding nozzle, comprising: an upper nozzle ring 12 and a lower nozzle ring 11 fixed on the volute by screws 22, a rotatable synchronous ring 15 is coaxially arranged on the upper nozzle ring 12, and the synchronous ring 15 It is arranged on a step of the upper nozzle ring 12, and the upper nozzle ring 12 can rotate around the step surface, and can drive two slider devices to move.
[0033] The present invention utilizes th...
PUM
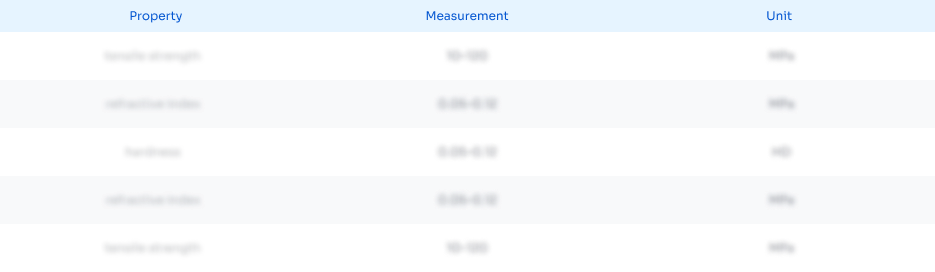
Abstract
Description
Claims
Application Information

- R&D
- Intellectual Property
- Life Sciences
- Materials
- Tech Scout
- Unparalleled Data Quality
- Higher Quality Content
- 60% Fewer Hallucinations
Browse by: Latest US Patents, China's latest patents, Technical Efficacy Thesaurus, Application Domain, Technology Topic, Popular Technical Reports.
© 2025 PatSnap. All rights reserved.Legal|Privacy policy|Modern Slavery Act Transparency Statement|Sitemap|About US| Contact US: help@patsnap.com