Passenger vehicle front floor framework structure
A skeleton structure and front floor technology, which is applied to the superstructure, superstructure sub-assemblies, vehicle components, etc., can solve the problems of insufficient living space for occupants, increased rearward movement of installation points, and vulnerable thighs, etc. The effect of structural deformation, reduction of deformation, and improvement of frontal collision performance
- Summary
- Abstract
- Description
- Claims
- Application Information
AI Technical Summary
Problems solved by technology
Method used
Image
Examples
Embodiment Construction
[0022] The present invention will be further described in detail below in conjunction with the accompanying drawings to facilitate a clearer understanding of the present invention, but they do not limit the present invention.
[0023] Such as figure 1 As shown, a front floor skeleton structure of a passenger car includes a left front side beam 1 and a right front side beam 2 under the front floor, and a left front side beam cover plate 19 is arranged on the left front side beam 1 , and the right front side beam 2 There is a right front longitudinal beam cover plate 20 on the top, the rear end of the left front longitudinal beam 1 is connected to the front floor left inner longitudinal beam 3, the rear end of the right front longitudinal beam 2 is connected to the front floor right inner longitudinal beam 4, and the left front longitudinal beam A dash panel beam 21 is connected between the rear end of the beam 1 and the rear end of the right front longitudinal beam 2, and a tra...
PUM
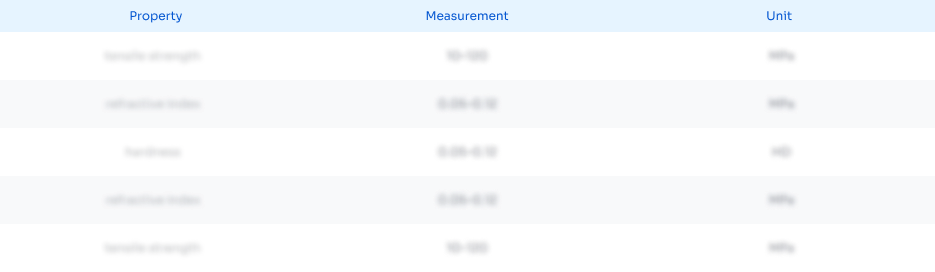
Abstract
Description
Claims
Application Information

- Generate Ideas
- Intellectual Property
- Life Sciences
- Materials
- Tech Scout
- Unparalleled Data Quality
- Higher Quality Content
- 60% Fewer Hallucinations
Browse by: Latest US Patents, China's latest patents, Technical Efficacy Thesaurus, Application Domain, Technology Topic, Popular Technical Reports.
© 2025 PatSnap. All rights reserved.Legal|Privacy policy|Modern Slavery Act Transparency Statement|Sitemap|About US| Contact US: help@patsnap.com