Ferrozirconium red material
A technology of red and iron zirconium, which is applied in the field of iron zirconium red material, can solve the problems that the composition and activity of fused zirconia cannot reach that of chemical zirconium, the high production cost of zirconium iron red material, and the high production cost of chemical zirconium, so as to achieve Good color effect, high wrapping rate, high activity effect
- Summary
- Abstract
- Description
- Claims
- Application Information
AI Technical Summary
Problems solved by technology
Method used
Image
Examples
Embodiment 1
[0024] The preparation method of activated zirconium dioxide is to mix 100Kg of zircon sand and 5Kg of carbon black, then sintering and calcining to obtain desiliconized zirconium. The zirconium sand is 80 meshes and the zirconium content is 66%. Then sodium hydroxide is added. Sodium zirconate is obtained by alkali fusion calcination. The calcination temperature of alkali fusion calcination is 1250℃. After the sodium zirconium is hydrolyzed, it is neutralized with hydrochloric acid to form zirconium hydroxide and sodium chloride. Then sodium hydroxide is added to control the pH at 8-9. After washing and removing sodium chloride, the material is dried to obtain active zirconium dioxide.
[0025] The active zirconium dioxide prepared in this embodiment is used in the production of zirconium iron red material.
[0026] A zirconium-iron red material prepared from raw materials with the following weight ratios: 20wt% silica, 10wt% ferric oxide, 0.5wt% potassium fluorosilicate, 2.5wt% m...
Embodiment 2
[0028] The preparation method of active zirconium dioxide is to mix 100Kg of zircon sand and 7.5Kg of graphite, then sintering and calcining to obtain desiliconized zirconium, the zircon sand is 100 mesh, the zirconium content is 68%, and then sodium hydroxide is added. Sodium zirconate is obtained by alkali fusion calcination. The calcination temperature of alkali fusion calcination is 1275℃. After sodium zirconium is hydrolyzed, it is neutralized with hydrochloric acid to form zirconium hydroxide and sodium chloride. Then sodium hydroxide is added to control the pH value at 8-9. After washing and removing sodium chloride, the material is dried to obtain active zirconium dioxide.
[0029] The active zirconium dioxide prepared in this embodiment is used in the production of zirconium iron red material.
[0030] A zirconium-iron red material prepared from raw materials with the following weight ratios: 28wt% silicon dioxide, 15wt% ferric oxide, 1wt% sodium fluorosilicate, 2wt% magne...
Embodiment 3
[0032] The preparation method of active zirconium dioxide is to mix 100Kg of zircon sand and 10Kg of water-washed coal, then sintering and calcining to obtain desiliconized zirconium. The zirconium sand is 120 meshes and the zirconium content is 70%. Then sodium carbonate is added for alkali Sodium zirconate is obtained by melting and calcination. The calcination temperature of alkali fusion and calcination is 1300℃. After sodium zirconium is hydrolyzed, sulfuric acid is added to neutralize to form zirconium hydroxide and sodium sulfate. Then sodium hydroxide is added to control the pH value at 8-9, and finally washed and removed. Dry the material after sodium sulfate to obtain active zirconium dioxide.
[0033] The active zirconium dioxide prepared in this embodiment is used in the production of zirconium iron red material.
[0034] A zirconium-iron red material prepared from raw materials with the following weight ratios: 23wt% silica, 11.5wt% ferric oxide, 2wt% sodium fluorosili...
PUM
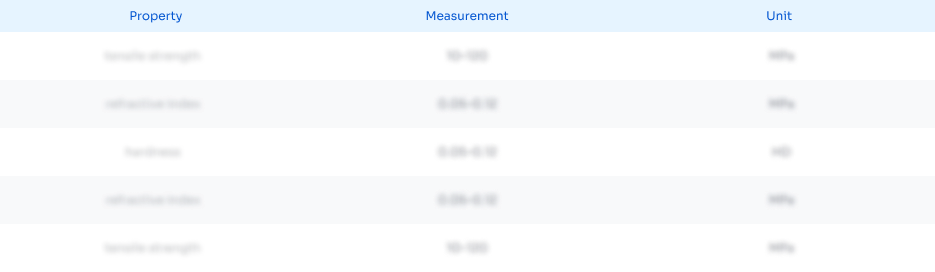
Abstract
Description
Claims
Application Information

- Generate Ideas
- Intellectual Property
- Life Sciences
- Materials
- Tech Scout
- Unparalleled Data Quality
- Higher Quality Content
- 60% Fewer Hallucinations
Browse by: Latest US Patents, China's latest patents, Technical Efficacy Thesaurus, Application Domain, Technology Topic, Popular Technical Reports.
© 2025 PatSnap. All rights reserved.Legal|Privacy policy|Modern Slavery Act Transparency Statement|Sitemap|About US| Contact US: help@patsnap.com