Engine Exhaust Manifolds and Flanges
An air intake flange and flange technology, which is applied to engine components, machines/engines, flange connections, etc., can solve the problems of poor coplanarity, easy resonance, air leakage and failure of split flanges, and improve the structure. Stiffness and strength, the effect of reducing local detachment and improving stress conditions
- Summary
- Abstract
- Description
- Claims
- Application Information
AI Technical Summary
Problems solved by technology
Method used
Image
Examples
Embodiment Construction
[0019] The present invention will be described in further detail below in conjunction with the accompanying drawings.
[0020] see figure 1 , the engine exhaust manifold includes a flange 1, an air channel 2, and a collecting pipe 3, wherein one end of the air channel is connected to the collecting pipe, and the other end is connected to the flange. The exhaust manifold provided by the present invention includes four air Road 2.
[0021] Such as figure 2 , image 3 As shown, the flange provided by the present invention includes an intake flange surface 11 connected to the cylinder head, and an air passage flange surface 12 located on the air passage side, and the flange body is provided with an air passage hole 15, so The air intake flange surface is provided with an integral convex surface 13 higher than the intake flange surface, the air passage holes 15 are distributed on the convex surface, and the flange 1 is provided with mounting holes 18, and the flange 1 passes th...
PUM
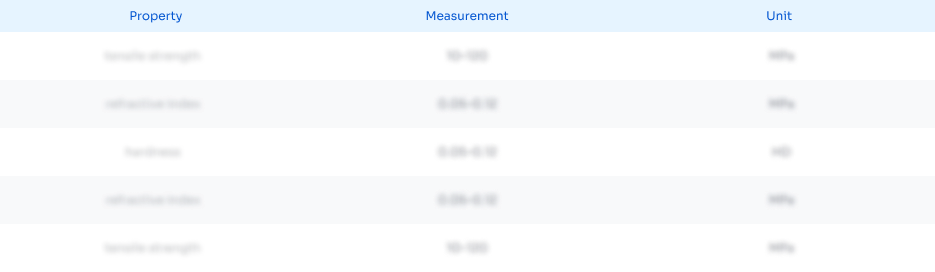
Abstract
Description
Claims
Application Information

- R&D Engineer
- R&D Manager
- IP Professional
- Industry Leading Data Capabilities
- Powerful AI technology
- Patent DNA Extraction
Browse by: Latest US Patents, China's latest patents, Technical Efficacy Thesaurus, Application Domain, Technology Topic, Popular Technical Reports.
© 2024 PatSnap. All rights reserved.Legal|Privacy policy|Modern Slavery Act Transparency Statement|Sitemap|About US| Contact US: help@patsnap.com