Process for circularly producing thermoplastic barium sulfate phenolic resin by precipitation method
A technology of phenolic resin and barium sulfate, which is applied in the field of cyclic production of thermoplastic barium sulfate phenolic resin by precipitation method, can solve the problems of slowing down the reaction speed, difficult to achieve satisfactory treatment effect, and affecting product preservation, so as to avoid the generation of waste water and benefit the environment The effect of protection and good economic benefits
- Summary
- Abstract
- Description
- Claims
- Application Information
AI Technical Summary
Problems solved by technology
Method used
Image
Examples
Embodiment 1
[0028] Example 1: Preparation of thermoplastic barium sulfate phenolic resin
[0029] The formulation of thermoplastic barium sulfate phenolic resin can be in the following range:
[0030]
[0031] Start the stirring of the 1000-liter reactor with condenser, stirrer, quick opening, jacket steam heating and water cooling, add 250Kg of phenol, 65Kg of solid formaldehyde, 250Kg of polycondensation dehydration fraction or deionized water, and turn on steam to heat to 50-80 After depolymerization of formaldehyde, 1Kg of sulfuric acid (50%) was slowly added, and the temperature was raised to reflux carefully. After the reaction was stable, 2Kg of remaining sulfuric acid (50%) was slowly added in two batches, and the sample was refluxed for 1 hour. The sample was collected at 20 ℃ When the water is not sticky and the hand is hard, the jacket is cooled to the material temperature of 96 ℃, and barium hydroxide (Ba(OH)) is slowly added. 2 *8H 2 0) 4.8Kg neutralize sulfuric acid, st...
Embodiment 2
[0032] Example 2: Preparation of low cardanol thermoplastic barium sulfate phenolic resin
[0033] Recipes can range from:
[0034]
[0035] Start the stirring of the 1000-liter reactor with condenser, stirrer, quick opening, jacket steam heating and water cooling, add 345Kg of phenol, 91Kg of solid formaldehyde, 59Kg of cardanol, and 345Kg of polycondensation dehydration fraction, and open the steam to heat to 50-80 After depolymerization of formaldehyde, 2.3Kg of sulfuric acid (50%) was slowly added, and the temperature was raised to reflux carefully. After the reaction was gentle, the remaining sulfuric acid (50%) 5.4.Kg was slowly added in two steps, and then refluxed for 1 hour and sampled. When the sample does not stick to the hand in 20°C water, the jacket is cooled to a material temperature of 95-96°C, and barium hydroxide (Ba(OH)) is slowly added. 2 *8H 2 O) 12.4Kg neutralize sulfuric acid, terminate catalytic reaction, generate barium sulfate precipitation and w...
Embodiment 3
[0036] Example 3. Preparation of high cardanol thermoplastic barium sulfate phenolic resin
[0037] Recipes can range from:
[0038]
[0039] Start the stirring of the 1000-liter reactor with condenser, stirrer, quick opening, jacket steam heating and water cooling, add 220Kg of phenol, 65Kg of solid formaldehyde, 72Kg of cardanol, polycondensation dehydration fraction and 220Kg of deionized water, turn on steam heating After depolymerizing the formaldehyde at 50~80℃, slowly add 2Kg of sulfuric acid (50%), and carefully heat up to reflux. After the reaction is flat, slowly add 6Kg of remaining sulfuric acid (50%) in two steps and reflux for 1 hour. , the sample is not sticky in water at 20°C and when the jacket is hard, the jacket is cooled to the material temperature of 96°C, and barium hydroxide (Ba(OH)) is slowly added. 2 *8H 20) 4.8Kg neutralize sulfuric acid, stop catalytic reaction, generate barium sulfate precipitation and water, then carry out vacuum dehydration w...
PUM
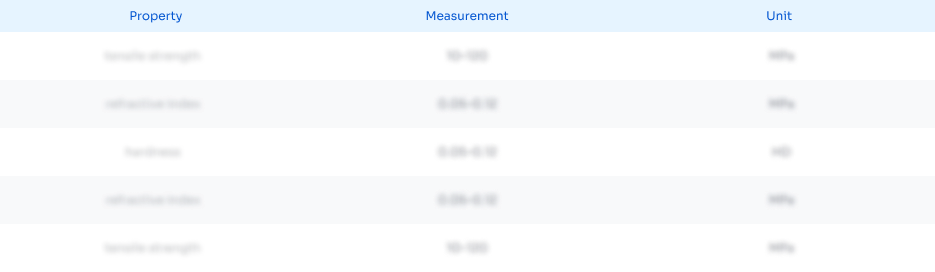
Abstract
Description
Claims
Application Information

- R&D
- Intellectual Property
- Life Sciences
- Materials
- Tech Scout
- Unparalleled Data Quality
- Higher Quality Content
- 60% Fewer Hallucinations
Browse by: Latest US Patents, China's latest patents, Technical Efficacy Thesaurus, Application Domain, Technology Topic, Popular Technical Reports.
© 2025 PatSnap. All rights reserved.Legal|Privacy policy|Modern Slavery Act Transparency Statement|Sitemap|About US| Contact US: help@patsnap.com