Fiber board and manufacturing method thereof
A production method and fiberboard technology, which can be applied to other seating furniture, mattresses, textiles, and papermaking, and can solve problems such as long insects, high sugar content in coconut palm fiber, and large contact area
- Summary
- Abstract
- Description
- Claims
- Application Information
AI Technical Summary
Problems solved by technology
Method used
Image
Examples
Embodiment 2
[0023] Since the fiberboard is composed of the first fiber layer 101 and the second fiber layer 102, the fiberboard may crack from the connection between the first fiber layer 101 and the second fiber layer 102 during long-term use. For this problem, optionally, the side walls of the first fiber layer 101 and the second fiber layer 102 are provided with a glue layer, so that the side walls of the first fiber layer 101 and the second fiber layer 102 can be bonded by the glue layer, Furthermore, the effect of closely bonding the entire first fiber layer 101 and the second fiber layer 102 is achieved, so as to solve the problem of cracking of the fiberboard.
[0024] The fiberboard of this embodiment sandwiches the second fiber layer 102 through the first fiber layer 101, so, in the process of specific setting, in order to make the first fiber layer 101 and the second fiber layer 102 can better realize Form an integral fiberboard, so in this embodiment, the first fiber layer 101 ...
PUM
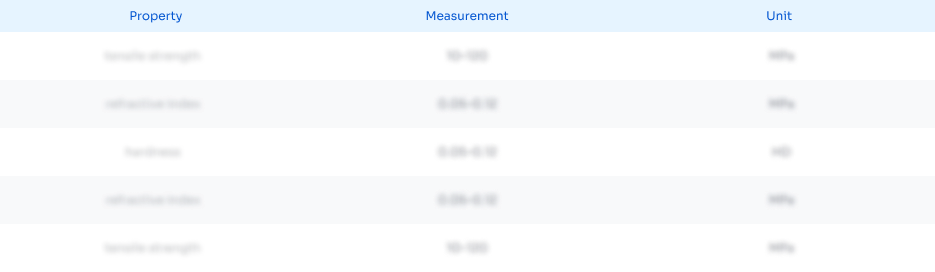
Abstract
Description
Claims
Application Information

- R&D
- Intellectual Property
- Life Sciences
- Materials
- Tech Scout
- Unparalleled Data Quality
- Higher Quality Content
- 60% Fewer Hallucinations
Browse by: Latest US Patents, China's latest patents, Technical Efficacy Thesaurus, Application Domain, Technology Topic, Popular Technical Reports.
© 2025 PatSnap. All rights reserved.Legal|Privacy policy|Modern Slavery Act Transparency Statement|Sitemap|About US| Contact US: help@patsnap.com