Low-voltage high-current ultrasonic impact apparatus
An ultrasonic shock and high current technology, applied in the field of mechanical structure fatigue improvement, can solve the problems of personal safety threats to operators, harsh frequency tracking conditions, and reduced effective power, so as to improve frequency tracking conditions, increase effective power output, and reduce Effect of Load Impedance
- Summary
- Abstract
- Description
- Claims
- Application Information
AI Technical Summary
Problems solved by technology
Method used
Image
Examples
Embodiment 1
[0040] For titanium alloy T-joints, the inner welding toe is treated with a low-voltage, high-current full-wavelength step-cone-step ultrasonic impact method, such as Figure 4 shown.
[0041] Experimental results: After treatment, the weld toe of the workpiece transitioned smoothly, and the roughness Ra of the treatment position was 0.46; the hardness of the sample increased significantly after treatment, and the surface hardness increased by about 1.6 times compared with the core part where the microstructure did not change; the surface hardness of the workpiece A residual compressive stress of 635MPa was formed. Fatigue strength increased by 56%.
Embodiment 2
[0043] The 16Mn pipe with a wall thickness of 30mm is surface treated with a low-voltage, high-current half-wavelength ultrasonic impact method, such as Figure 5 shown.
[0044] Experimental results: After treatment, the weld toe of the workpiece transitions smoothly, and the roughness Ra of the treated position is 0.34; the surface hardness is increased by about 1.7 times; the residual compressive stress of 746MPa is formed on the surface of the workpiece. Fatigue strength increased by 91%.
PUM
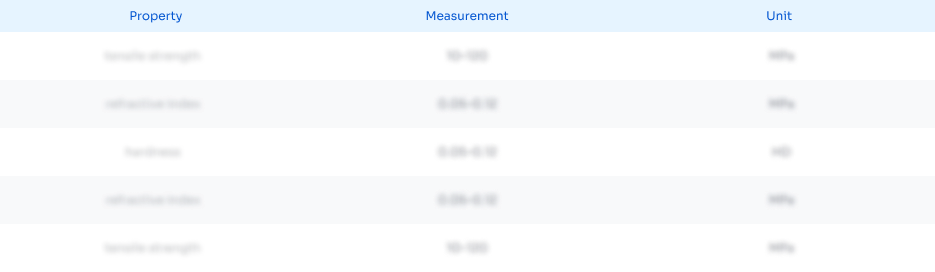
Abstract
Description
Claims
Application Information

- R&D
- Intellectual Property
- Life Sciences
- Materials
- Tech Scout
- Unparalleled Data Quality
- Higher Quality Content
- 60% Fewer Hallucinations
Browse by: Latest US Patents, China's latest patents, Technical Efficacy Thesaurus, Application Domain, Technology Topic, Popular Technical Reports.
© 2025 PatSnap. All rights reserved.Legal|Privacy policy|Modern Slavery Act Transparency Statement|Sitemap|About US| Contact US: help@patsnap.com