Method for producing hot-box resin for casting
A production method and hot core box technology, which are applied in casting molding equipment, casting molds, cores, etc., can solve the problems of fast gas generation, unstable strength, and inability to overcome, and achieve improved product performance, smooth appearance, Fast curing effect
- Summary
- Abstract
- Description
- Claims
- Application Information
AI Technical Summary
Problems solved by technology
Method used
Examples
Embodiment 1
[0027] Embodiment 1: A production method of hot box resin for casting, characterized in that: the weight percentage of its raw materials is: formaldehyde aqueous solution: 45%, urea: 4%, phenol: 18%, furfuryl alcohol: 57%, Modifier: 2%, enhancer 0.4%
[0028] Its method comprises the following steps:
[0029] a. Heat and dissolve the above-mentioned amount of phenol, add it into the reaction kettle, start the mixer, add the above-mentioned amount of formaldehyde solution and furfuryl alcohol in turn, and use NaOH lye to bring the pH value of the feed solution to 9-10;
[0030] b. Open the steam valve, raise the temperature to 90-95°C within 40-60 minutes, and keep the temperature for 60 minutes;
[0031] c. Add 1 / 2 of the amount of NaOH lye in the first step, at 90-95°C, keep the temperature for 30 minutes;
[0032] d. After the heat preservation is over, lower the temperature to 80°C, adjust the pH value to 4.5-5.5 with formic acid, and vacuum dehydrate. The dehydration amo...
Embodiment 2
[0038] Embodiment 2: A kind of production method of casting hot box resin, it is characterized in that: the weight percentage of its raw material is: formaldehyde aqueous solution: 55%, urea: 6%, phenol: 22%, furfuryl alcohol: 48%, Modifier: 4%, enhancer 0.6%
[0039] Its method comprises the following steps:
[0040] a. Heat and dissolve the above-mentioned amount of phenol, add it into the reaction kettle, start the mixer, add the above-mentioned amount of formaldehyde solution and furfuryl alcohol in turn, and use NaOH lye to bring the pH value of the feed solution to 9-10;
[0041] b. Open the steam valve, raise the temperature to 90-95°C within 40-60 minutes, and keep the temperature for 60 minutes;
[0042] c. Add 1 / 2 of the amount of NaOH lye in the first step, at 90-95°C, keep the temperature for 30 minutes;
[0043] d. After the heat preservation is over, lower the temperature to 80°C, adjust the pH value to 4.5-5.5 with formic acid, and vacuum dehydrate. The dehydr...
Embodiment 3
[0049] Embodiment 3: A production method of hot box resin for casting, characterized in that: the weight percentage of its raw materials is: formaldehyde aqueous solution: 65%, urea: 8%, phenol: 26%, furfuryl alcohol: 39%, Modifier: 6%, enhancer 0.8%
[0050] Its method comprises the following steps:
[0051] a. Heat and dissolve the above-mentioned amount of phenol, add it into the reaction kettle, start the mixer, add the above-mentioned amount of formaldehyde solution and furfuryl alcohol in turn, and use NaOH lye to bring the pH value of the feed solution to 9-10;
[0052]b. Open the steam valve, raise the temperature to 90-95°C within 40-60 minutes, and keep the temperature for 60 minutes;
[0053] c. Add 1 / 2 of the amount of NaOH lye in the first step, at 90-95°C, keep the temperature for 30 minutes;
[0054] d. After the heat preservation is over, lower the temperature to 80°C, adjust the pH value to 4.5-5.5 with formic acid, and vacuum dehydrate. The dehydration amou...
PUM
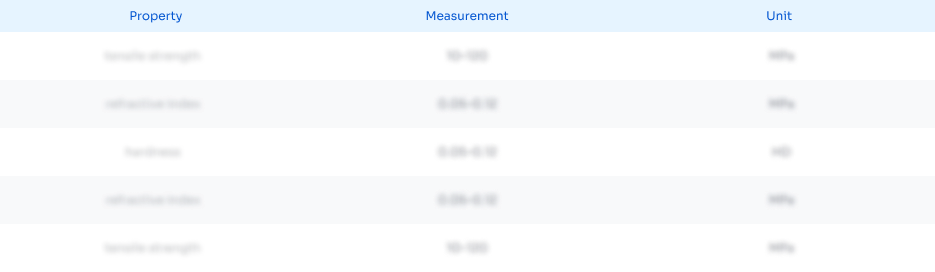
Abstract
Description
Claims
Application Information

- R&D
- Intellectual Property
- Life Sciences
- Materials
- Tech Scout
- Unparalleled Data Quality
- Higher Quality Content
- 60% Fewer Hallucinations
Browse by: Latest US Patents, China's latest patents, Technical Efficacy Thesaurus, Application Domain, Technology Topic, Popular Technical Reports.
© 2025 PatSnap. All rights reserved.Legal|Privacy policy|Modern Slavery Act Transparency Statement|Sitemap|About US| Contact US: help@patsnap.com