Method for controlling convexity of single-rack double-coiler aluminum hot mill
A control method and double coiling technology, applied in contour control and other directions, can solve the problems of inability to control convexity, inability to control good plate shape, and unfavorable product quality.
- Summary
- Abstract
- Description
- Claims
- Application Information
AI Technical Summary
Problems solved by technology
Method used
Image
Examples
Embodiment Construction
[0078] The present invention performs setting calculation and feedback control on the crown of the roll to be rolled to ensure the consistency of the crown within the entire length of the strip under the premise of good flatness of the exit strip, thereby overcoming the limitation of manual experience control of the strip shape shortcoming. The main method steps are as follows:
[0079] (1) Overall convexity control strategy formulation.
[0080] The overall crown control strategy is to solve the problem of how to exert the maximum effect of these control means on the premise of the existing strip shape control means to avoid unreasonable use of bending force and cooling spray, so as to achieve the purpose of the present invention.
[0081] Since the crown control of the present invention is carried out on the premise of ensuring good straightness of the exit, the number of passes for crown feedback to be put into use is limited by factors such as product thickness and produc...
PUM
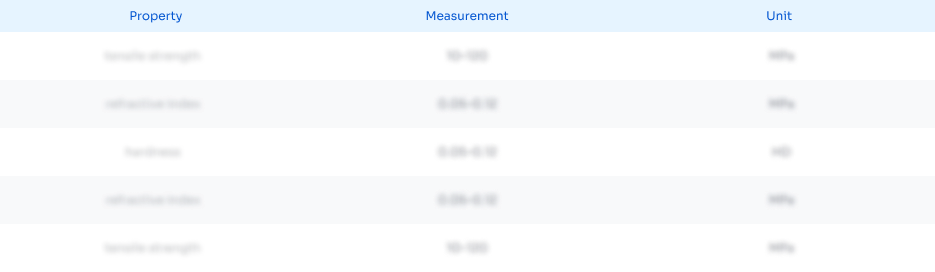
Abstract
Description
Claims
Application Information

- Generate Ideas
- Intellectual Property
- Life Sciences
- Materials
- Tech Scout
- Unparalleled Data Quality
- Higher Quality Content
- 60% Fewer Hallucinations
Browse by: Latest US Patents, China's latest patents, Technical Efficacy Thesaurus, Application Domain, Technology Topic, Popular Technical Reports.
© 2025 PatSnap. All rights reserved.Legal|Privacy policy|Modern Slavery Act Transparency Statement|Sitemap|About US| Contact US: help@patsnap.com