Profile steel rolling production line and production method thereof
A production line and section steel technology, applied in metal rolling and other directions, can solve the problems of increasing the length of the conveyor roller table, construction investment, construction engineering quantity workshop production energy consumption and production cost, so as to reduce the equipment failure rate and improve the roller Rotation flexibility and the effect of reducing engineering construction investment
- Summary
- Abstract
- Description
- Claims
- Application Information
AI Technical Summary
Problems solved by technology
Method used
Image
Examples
Embodiment 1
[0025] figure 1 It is the process equipment layout diagram of embodiment 1 of the present invention, as figure 1 As shown, the section steel rolling production line of the present invention comprises a heating unit 1, a rough rolling unit, an intermediate rolling unit, a finish rolling unit and a finishing unit 13 arranged in sequence, and the rough rolling unit includes a rough rolling mill 2 and a rough There are the same number of driving devices I3 in the rolling mill 2, the driving device I3 drives the roughing mill 2 to move axially along the rolls of the roughing mill, and the rolls of the roughing mill 2 are sequentially provided with more than two rolling grooves with different slot holes along the axial direction; The intermediate rolling unit includes one intermediate rolling mill 4 and the same number of driving devices II5 as the intermediate rolling mill 4, the driving device II5 drives the intermediate rolling mill 4 to move axially along the intermediate rollin...
Embodiment 2
[0030] figure 2 It is the process equipment layout diagram of embodiment 2 of the present invention, as figure 2 As shown, the section steel rolling production line of the present invention comprises a heating unit 1, a rough rolling unit, an intermediate rolling unit, a finish rolling unit and a finishing unit 13 arranged in sequence, and the rough rolling unit includes a rough rolling mill 2 and a rough There are the same number of driving devices I3 in the rolling mill 2, the driving device I3 drives the roughing mill 2 to move axially along the rolls of the roughing mill, and the rolls of the roughing mill 2 are sequentially provided with more than two rolling grooves with different slot holes along the axial direction; The intermediate rolling unit includes two intermediate rolling mills 4 and the same number of driving devices II5 as the intermediate rolling mills 4. The driving device II5 drives the intermediate rolling mills 4 to move axially along the intermediate r...
Embodiment 3
[0035] image 3 It is the process equipment layout diagram of embodiment 3 of the present invention, as image 3As shown, the section steel rolling production line of the present invention comprises a heating unit 1, a rough rolling unit, an intermediate rolling unit, a finish rolling unit and a finishing unit 13 arranged in sequence, and the rough rolling unit includes a rough rolling mill 2 and a rough There are the same number of driving devices I3 in the rolling mill 2, the driving device I3 drives the roughing mill 2 to move axially along the rolls of the roughing mill, and the rolls of the roughing mill 2 are sequentially provided with more than two rolling grooves with different slot holes along the axial direction; The intermediate rolling unit includes one intermediate rolling mill 4 and the same number of driving devices II5 as the intermediate rolling mill 4, the driving device II5 drives the intermediate rolling mill 4 to move axially along the intermediate rolling...
PUM
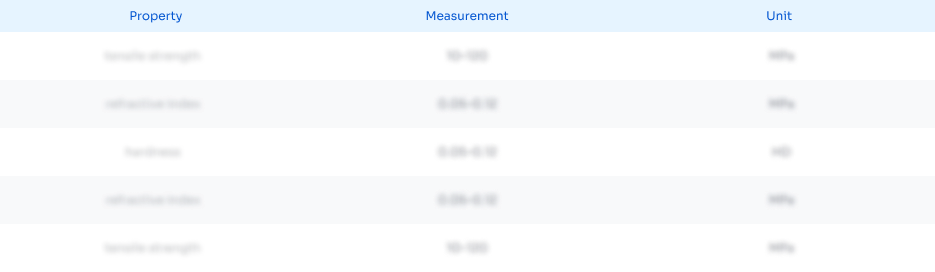
Abstract
Description
Claims
Application Information

- R&D Engineer
- R&D Manager
- IP Professional
- Industry Leading Data Capabilities
- Powerful AI technology
- Patent DNA Extraction
Browse by: Latest US Patents, China's latest patents, Technical Efficacy Thesaurus, Application Domain, Technology Topic, Popular Technical Reports.
© 2024 PatSnap. All rights reserved.Legal|Privacy policy|Modern Slavery Act Transparency Statement|Sitemap|About US| Contact US: help@patsnap.com