Integral forming method for sewing enhanced cross connector made of fiber reinforced resin matrix composite
A fiber-reinforced resin and composite material technology, applied in the field of composite material manufacturing, can solve problems such as weak strength and achieve the effect of improving interlayer strength
- Summary
- Abstract
- Description
- Claims
- Application Information
AI Technical Summary
Problems solved by technology
Method used
Image
Examples
Embodiment Construction
[0019] The present invention will be further described below in conjunction with the accompanying drawings and implementation examples.
[0020] The flow chart of the present invention is as figure 1 As shown, the cross-shaped fiber preform is prepared first, and then the cross-shaped fiber preform is stitched and reinforced by unidirectional fiber threads, and then the cross-shaped fiber preform after sewing is put into the mold and positioned for mold clamping , and then vacuumize, inject resin, heat up and solidify, and finally open the mold to take out the solidified sewing-reinforced fiber-reinforced resin-based composite material cross joint. exist figure 2 Among them, the sewing-reinforced fiber-reinforced resin-based composite cross-shaped joint is composed of an upper T-shaped laminate 1, a lower T-shaped laminate 2, an intermediate laminate 3, a triangular area 4 and a sewing fiber thread 5, and the triangular area 4 is made of Unidirectional fiber bundles for fil...
PUM
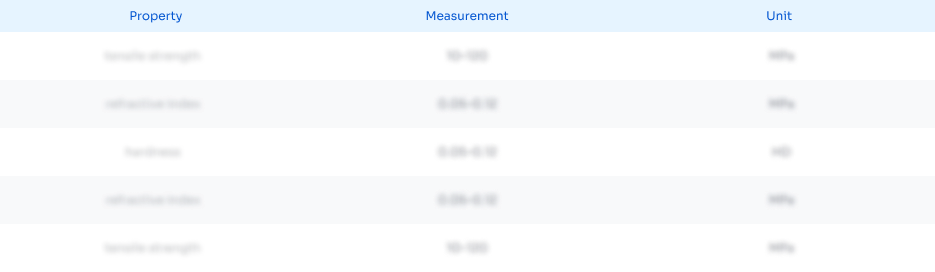
Abstract
Description
Claims
Application Information

- Generate Ideas
- Intellectual Property
- Life Sciences
- Materials
- Tech Scout
- Unparalleled Data Quality
- Higher Quality Content
- 60% Fewer Hallucinations
Browse by: Latest US Patents, China's latest patents, Technical Efficacy Thesaurus, Application Domain, Technology Topic, Popular Technical Reports.
© 2025 PatSnap. All rights reserved.Legal|Privacy policy|Modern Slavery Act Transparency Statement|Sitemap|About US| Contact US: help@patsnap.com