Continuous casting method of dissimilar stainless steel
A stainless steel and continuous casting technology, applied in the field of dissimilar stainless steel continuous casting, can solve the problems of increased labor intensity of workers, low number of tundish continuous casting furnaces, and low operation rate of continuous casting machines, so as to improve continuous casting productivity and increase medium The effect of enclosing the number of continuous pouring furnaces and improving the operation rate of equipment
- Summary
- Abstract
- Description
- Claims
- Application Information
AI Technical Summary
Problems solved by technology
Method used
Image
Examples
Embodiment 1
[0032] This embodiment is the actual production situation of 430 and 0Cr13R continuous casting of different steel types in the same tundish, with 430 in front and 0Cr13R in the back. The section of the two steel types is 1240mm, and the mass percentages of the two steel types are as follows:
[0033] The mass percent of the composition of 430 is:
[0034] C: 0.030-0.060; Si: 0.20-0.50; Mn: 0.30-0.50; Cr: 16.00-16.80;
[0035] The rest is Fe and inevitable impurity elements.
[0036] The target temperature for the 430 is 1525-1535°C.
[0037] The mass percentage of the composition of 0Cr13R is:
[0038] C: 0.02-0.03; Si: 0.25-0.35; Mn: 0.20-0.30; Cr: 12.00-12.50;
[0039] The rest is Fe and inevitable impurity elements.
[0040] The target temperature for 0Cr13R is 1530-1540°C.
[0041] The steps of this embodiment are:
[0042] Ⅰ When the previous furnace of molten steel (430 steel grade) was pulled to the end of ladle pouring, when the tundish molten steel was displ...
Embodiment 2
[0057] This embodiment is the actual production situation of continuous casting of different steel types in the same tundish of 316L and 301B, with 316L at the front and 301B at the back. The cross-section of the two steel grades is 1535mm, and the mass percentages of the components of the two steel grades are as follows:
[0058] The mass percentage of the composition of 316L is:
[0059] C: 0.015-0.025; Si: 0.40-0.60; Mn: 1.10-1.30;
[0060] Cr: 16.50-16.80; Ni: 10.05-10.15; Mo: 2.00-3.00;
[0061] The rest is Fe and unavoidable impurities.
[0062] The target temperature for 316L is 1485-1495°C.
[0063] The mass percentage of the composition of 301B is:
[0064] C: 0.10-0.13; Si: 0.60-0.90; Mn: 0.65-0.90;
[0065] Cr: 16.30-16.65; Ni: 6.65-6.85; Mo≤0.40;
[0066] The rest is Fe and unavoidable impurities.
[0067] The target temperature for 301B is 1490-1500°C.
[0068] The steps of this embodiment are:
[0069] Ⅰ When the ladle of the previous furnace of molte...
Embodiment 3
[0086] This embodiment is the actual production situation of continuous casting of different steel types in the same tundish of 409 and 430, 409 is in front and 430 is in the back. The cross-section of the two steel grades is 1535mm, and the mass percentages of the components of the two steel grades are as follows:
[0087] The mass percent of the composition of 409 is:
[0088] C≤0.001; Si: 0.30-0.50; Mn: 0.10-0.30;
[0089] Cr: 11.00-11.30; Ti: 0.10-0.23; N≤0.010;
[0090] The rest is Fe and unavoidable impurities.
[0091] The target temperature for 409 is 1545-1555°C.
[0092] The mass percent of the composition of 430 is:
[0093] C: 0.030-0.060; Si: 0.20-0.50; Mn: 0.30-0.50;
[0094] Cr: 16.00-16.80; Ti≤0.010; N≤0.060;
[0095] The rest is Fe and unavoidable impurities.
[0096] The target temperature for the 430 is 1525-1535°C.
[0097] The steps of this embodiment are:
[0098] Ⅰ When the previous furnace of molten steel (409) was finished pouring in the la...
PUM
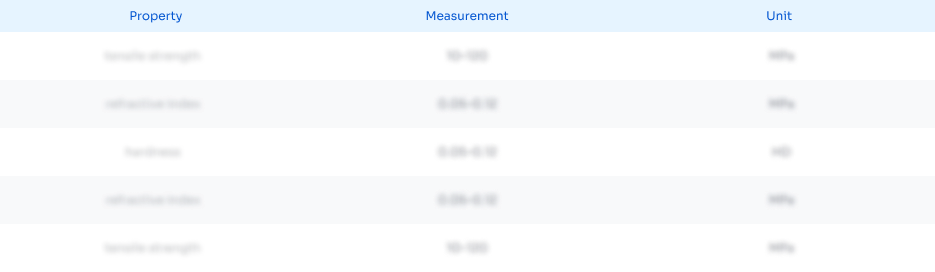
Abstract
Description
Claims
Application Information

- R&D
- Intellectual Property
- Life Sciences
- Materials
- Tech Scout
- Unparalleled Data Quality
- Higher Quality Content
- 60% Fewer Hallucinations
Browse by: Latest US Patents, China's latest patents, Technical Efficacy Thesaurus, Application Domain, Technology Topic, Popular Technical Reports.
© 2025 PatSnap. All rights reserved.Legal|Privacy policy|Modern Slavery Act Transparency Statement|Sitemap|About US| Contact US: help@patsnap.com