Grooving perpendicularity control process of super-deep underground diaphragm wall
A verticality and trough-forming technology, which is applied to artificial islands, water conservancy projects, underwater structures, etc., can solve problems such as inability to carry out construction and difficulty in placing steel cages in place, and achieve the effect of shortening construction time
- Summary
- Abstract
- Description
- Claims
- Application Information
AI Technical Summary
Problems solved by technology
Method used
Image
Examples
Embodiment Construction
[0014] The present invention will be further described below in conjunction with embodiment.
[0015] The ultra-deep underground diaphragm wall groove verticality control process uses hydraulic grabs to excavate to form grooves. Such as figure 1 As shown, before excavation, firstly, two sections of guide walls 2 are set according to the width of the slot 1 , and the distance between the two sections of guide walls 2 is the same as the width of the slot 1 . The guide wall 2 extends 1-1.5 meters deep from the ground to the ground. Utilize the wire rope 3 to hang the hydraulic grab bucket 4, so that the hydraulic grab bucket 4 is excavated between the two sections of guide walls 2. In the groove forming process, when the depth of the groove is less than 5-15 meters, the distance between the two sections of the guide wall 2 and the steel wire rope 3 is measured with a measuring stick. If the distance between the wire rope 3 and the two sections of the guide wall 2 is equal or t...
PUM
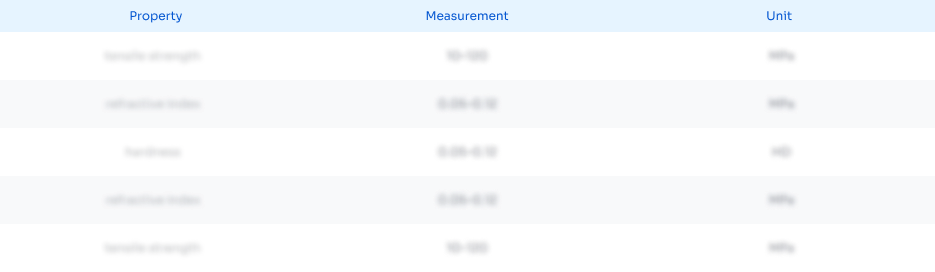
Abstract
Description
Claims
Application Information

- R&D
- Intellectual Property
- Life Sciences
- Materials
- Tech Scout
- Unparalleled Data Quality
- Higher Quality Content
- 60% Fewer Hallucinations
Browse by: Latest US Patents, China's latest patents, Technical Efficacy Thesaurus, Application Domain, Technology Topic, Popular Technical Reports.
© 2025 PatSnap. All rights reserved.Legal|Privacy policy|Modern Slavery Act Transparency Statement|Sitemap|About US| Contact US: help@patsnap.com