Preparation method of sucrose ester
A technology of sucrose ester and sucrose, applied in the field of non-ionic surfactants, can solve the problems of unguaranteed product quality, complicated separation and purification steps, easy to generate a large amount of waste water, etc., to achieve product safety, simple pretreatment method, and satisfactory Purity and non-toxic properties of the required effect
- Summary
- Abstract
- Description
- Claims
- Application Information
AI Technical Summary
Problems solved by technology
Method used
Image
Examples
Embodiment 1
[0022] Add 4g of calcium oxide as a dewatering agent to 30g of methyl stearate, stir to remove a small amount of water and free fatty acids in the methyl stearate, and then transfer the dehydrated methyl stearate to a three-necked bottle Add 51g of crushed and ground sucrose, use 3.2g of calcium oxide as a catalyst, quickly stir and evenly disperse for 30 minutes, adjust and set the oil bath temperature to 130°C, synthesize sucrose ester under normal pressure or reduced pressure, continue stirring, Stop heating after 4 hours of reaction, filter the product to remove the catalyst, transfer the reaction liquid to a separatory funnel, let stand for stratification, remove the lower aqueous phase, and then wash the upper oil phase with distilled water until it is neutral, and then The product is distilled under reduced pressure at 80°C to obtain pure sucrose ester.
Embodiment 2
[0024] Add 6g of calcium oxide as a dewatering agent to 36g of methyl stearate, stir to remove a small amount of water and free fatty acids in the methyl stearate, and then transfer the dehydrated methyl stearate to a three-necked bottle Add 103g of crushed and ground sucrose, use 6.9g of calcium oxide as a catalyst, quickly stir and uniformly disperse for 30 minutes, adjust and set the oil bath temperature to 90℃, synthesize sucrose ester under normal pressure or reduced pressure, continue stirring, After 2 h of reaction, stop heating, filter the product to remove solid catalyst, transfer the reaction liquid to a separatory funnel, let stand for stratification, remove the lower water phase, and then wash the upper oil phase with distilled water until it is neutral, then The product is distilled under reduced pressure at 80°C to obtain pure sucrose ester.
Embodiment 3
[0026] Add 7g of calcium oxide as a water remover to 42g of methyl stearate, stir to remove a small amount of water and free fatty acids in the methyl stearate, and then transfer the dehydrated methyl stearate to a three-necked bottle Add 217g of crushed and ground sucrose, use 15.5g of calcium oxide as a catalyst, quickly stir and evenly disperse for 30 minutes, adjust and set the oil bath temperature to 160°C, synthesize sucrose ester under normal pressure or reduced pressure, continue stirring After the reaction has proceeded for 42 hours, stop heating, filter the product to remove the solid catalyst, transfer the reaction liquid to a separatory funnel, stand for stratification, remove the lower aqueous phase, and then wash the upper oil phase with distilled water until it is neutral, then The product is distilled under reduced pressure at 80°C to obtain pure sucrose ester.
PUM
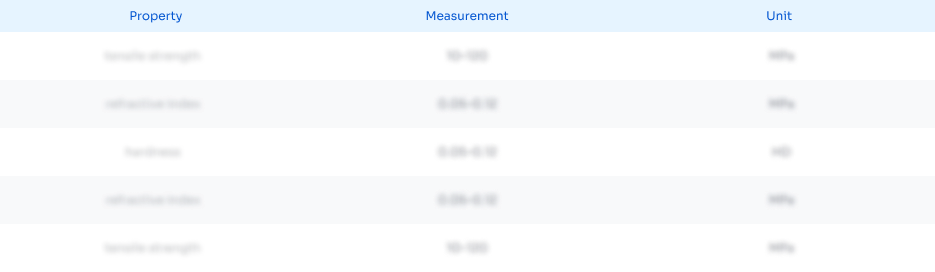
Abstract
Description
Claims
Application Information

- R&D
- Intellectual Property
- Life Sciences
- Materials
- Tech Scout
- Unparalleled Data Quality
- Higher Quality Content
- 60% Fewer Hallucinations
Browse by: Latest US Patents, China's latest patents, Technical Efficacy Thesaurus, Application Domain, Technology Topic, Popular Technical Reports.
© 2025 PatSnap. All rights reserved.Legal|Privacy policy|Modern Slavery Act Transparency Statement|Sitemap|About US| Contact US: help@patsnap.com