Polyethylene high-ratio foamed material and preparation method thereof
A foaming material and polyethylene technology, applied in the field of polyethylene high-rate foaming materials and their preparation, can solve the problems of poor sealing, high cost, low magnification, etc., and achieve reduced process costs and good sealing. good shock absorption and noise reduction effect
- Summary
- Abstract
- Description
- Claims
- Application Information
AI Technical Summary
Problems solved by technology
Method used
Examples
Embodiment 1
[0016] Embodiment 1: First take by weight percentage: 10% EPDM, 50% polyethylene, 5% stearic acid, 10% zinc oxide and 25% nitrogen dicarbonamide, then first 10% Put the EPDM into the pressurized internal mixing kneader for internal mixing, control the temperature in the mixing process at 80 degrees, make the EPDM in a hot melt state, and then put 50% polyethylene into the kneader to make the polyethylene Ethylene was kneaded in it for 10 minutes, then 5% stearic acid was added to continue kneading for 10 minutes, 10% zinc oxide was added to knead for 5 minutes, and 25% nitrogen dicarbonamide was added to continue kneading for 15 minutes , stop mixing, take out the mixed material, and then pour the kneaded mixed material into the double-pull granulator with a bucket elevator for granulation. After the granulation is completed, put the granules into the extruder to extrude. The extruded sheet is calendered by the calender at the same time, and finally the calendered sheet enters...
Embodiment 2
[0017] Embodiment 2: first take by weight percentage: 15% EPDM, 45% polyethylene, 8% stearic acid, 5% zinc oxide and 27% nitrogen diformamide, then first 15% Put the EPDM into the pressurized internal mixing kneader for internal mixing, control the temperature of the mixing process at 90 degrees, make the EPDM in a hot melt state, and then put 45% polyethylene into the kneader to make the polyethylene Ethylene was kneaded in it for 12 minutes, then 8% stearic acid was added to continue kneading for 5 minutes, 5% zinc oxide was added to knead for 8 minutes, and finally 27% nitrogen diformamide was added to knead for 18 minutes , stop mixing, take out the mixed material, and then pour the kneaded mixed material into the double-pull granulator with a bucket elevator for granulation. After the granulation is completed, put the granules into the extruder to extrude. The extruded sheet is calendered by the calender at the same time, and finally the calendered sheet enters the automa...
Embodiment 3
[0018] Embodiment 3: first take by weight percentage: 20% EPDM, 40% polyethylene, 2% stearic acid, 5% zinc oxide and 33% nitrogen diformamide, then first 20% Put the EPDM into the pressurized internal mixing kneader for internal mixing, control the temperature in the mixing process at 95 degrees, make the EPDM in a hot melt state, and then put 40% polyethylene into the kneader to make the polyethylene Ethylene was kneaded in it for 13 minutes, then 2% stearic acid was added to continue kneading for 5 minutes, 5% zinc oxide was added to knead for 7 minutes, and finally 33% nitrogen diformamide was added to knead for 17 minutes , stop mixing, take out the mixed material, and then pour the kneaded mixed material into the double-pull granulator with a bucket elevator for granulation. After the granulation is completed, put the granules into the extruder to extrude. The extruded sheet is calendered by the calender at the same time, and finally the calendered sheet enters the automa...
PUM
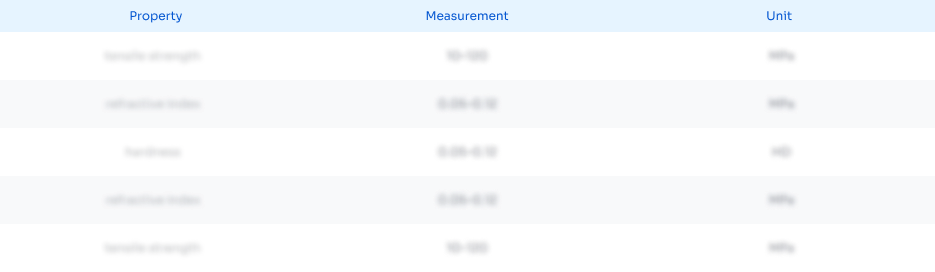
Abstract
Description
Claims
Application Information

- Generate Ideas
- Intellectual Property
- Life Sciences
- Materials
- Tech Scout
- Unparalleled Data Quality
- Higher Quality Content
- 60% Fewer Hallucinations
Browse by: Latest US Patents, China's latest patents, Technical Efficacy Thesaurus, Application Domain, Technology Topic, Popular Technical Reports.
© 2025 PatSnap. All rights reserved.Legal|Privacy policy|Modern Slavery Act Transparency Statement|Sitemap|About US| Contact US: help@patsnap.com