Capacitive micro inertial sensor with self calibration function
A technology of inertial sensors and capacitors, applied in the direction of testing/calibration of instruments, speed/acceleration/shock measuring equipment, and measuring devices, etc., can solve problems such as complicated operation and high cost, and achieve simple manufacturing process, high yield rate, and structural novel effect
- Summary
- Abstract
- Description
- Claims
- Application Information
AI Technical Summary
Problems solved by technology
Method used
Image
Examples
Embodiment Construction
[0017] The present invention will be further described below in conjunction with the embodiments and accompanying drawings, but the present invention is by no means limited to the described embodiments.
[0018] The invention provides a high-precision micro-inertial sensor with a self-calibration structure. The quality of the sensor chip can be improved by adopting a bulk silicon micro-machining process, thereby reducing noise, improving stability, and increasing sensitivity. The disadvantage is that the volume is slightly larger, but high-precision micromechanical inertial sensors can be produced. In order to reduce the driving voltage when driving the sensitive mass so that the driving voltage does not exceed the working voltage of the sensor, the mechanical noise and circuit noise can be reduced by increasing the static driving capacitance of the sensor. For comb-shaped capacitive sensors processed by bulk silicon technology such as Deep Reactive Particle Etching (Deep RIE)...
PUM
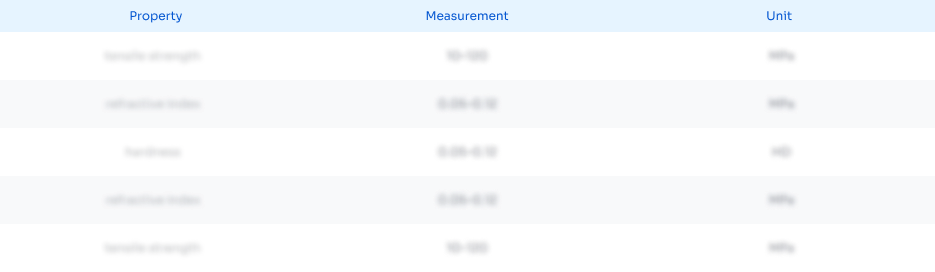
Abstract
Description
Claims
Application Information

- R&D
- Intellectual Property
- Life Sciences
- Materials
- Tech Scout
- Unparalleled Data Quality
- Higher Quality Content
- 60% Fewer Hallucinations
Browse by: Latest US Patents, China's latest patents, Technical Efficacy Thesaurus, Application Domain, Technology Topic, Popular Technical Reports.
© 2025 PatSnap. All rights reserved.Legal|Privacy policy|Modern Slavery Act Transparency Statement|Sitemap|About US| Contact US: help@patsnap.com