Method of controlling reference grinding position for rail welding joint refiner
A technology of reference position and welding joint, which is applied in the direction of track, track laying, track maintenance, etc., can solve the problems of inaccurate determination of reference position, easy generation of error signals, and inconvenient use, etc. Determine the exact effect
- Summary
- Abstract
- Description
- Claims
- Application Information
AI Technical Summary
Problems solved by technology
Method used
Examples
Embodiment 1
[0020] A specific embodiment of the present invention is a method for controlling the grinding reference position of a rail welded joint refiner; the method is as follows:
[0021] Initially, the grinding wheel faces the non-welding seam of the rail grinding area, the PLC controls the rotation of the grinding servo motor, and the grinding servo motor drives the grinding wheel to rotate; then the PLC controls the feed servo motor to reverse to make the feed mechanism drop vertically; when grinding When the armature current value of the grinding servo motor measured by the armature current sensor of the servo motor reaches the preset threshold value; the PLC controls the feeding servo motor to stop, and the PLC records the vertical position of the feeding mechanism at this time as the reference position for grinding ;
[0022] Then, the PLC controls the forward rotation of the feed servo motor so that the feed mechanism rises vertically by 0.5-0.8 mm to reach the grinding zero p...
Embodiment 2
[0025] The second specific embodiment of the present invention is a method for controlling the grinding reference position of a rail welded joint refiner; the method is as follows:
[0026] Initially, when the grinding wheel faces the non-weld seam of the rail grinding area, the PLC controls the rotation of the grinding servo motor, and the grinding servo motor drives the grinding wheel to rotate; then the PLC controls the piston rod of the lifting cylinder to drop to drive the feed mechanism to drop vertically; when grinding When the armature current value of the grinding servo motor measured by the servo motor armature current sensor reaches the preset threshold; the PLC controls the piston rod of the lifting cylinder to stop, and the PLC records the vertical position of the feeding mechanism at this time as the grinding benchmark Location;
[0027] Then, the PLC controls the piston rod of the lifting cylinder to rise to make the feed mechanism rise vertically by 0.5-0.8mm t...
PUM
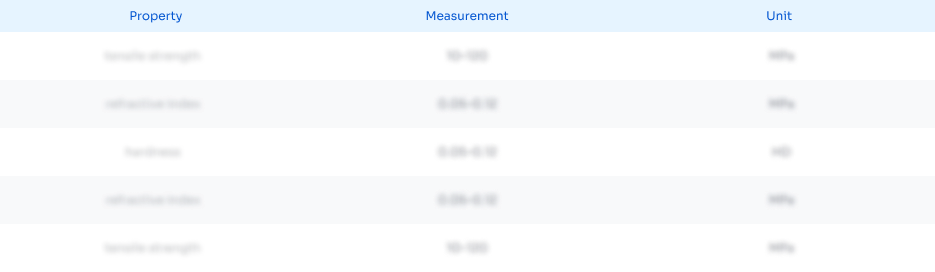
Abstract
Description
Claims
Application Information

- R&D Engineer
- R&D Manager
- IP Professional
- Industry Leading Data Capabilities
- Powerful AI technology
- Patent DNA Extraction
Browse by: Latest US Patents, China's latest patents, Technical Efficacy Thesaurus, Application Domain, Technology Topic, Popular Technical Reports.
© 2024 PatSnap. All rights reserved.Legal|Privacy policy|Modern Slavery Act Transparency Statement|Sitemap|About US| Contact US: help@patsnap.com