Loading sand-discharging system for float glass production line
A float glass and production line technology, applied in conveyor control devices, conveyor objects, conveyors, etc., can solve the problems of wasting time and reducing sand unloading efficiency, and achieve the effect of improving work efficiency and saving manpower and time.
- Summary
- Abstract
- Description
- Claims
- Application Information
AI Technical Summary
Problems solved by technology
Method used
Image
Examples
Embodiment Construction
[0008] Such as figure 1 As shown, the present invention consists of a sand unloading system and a feeding system. The sand unloading system consists of a hopper lifter 1, a belt discharge belt 2, a discharge trolley 3, a sand rake machine 4, an iron remover 5, a collection belt 6, The transfer belt 7 is composed of a PLC controller. One end of the belt discharge belt 2 is located at the discharge port of the upper hopper elevator 1, the discharge trolley 3 is installed on the belt discharge belt 2, and the sand raking machine 4 is located on the belt discharge belt 2. One end of the collection belt 6 is located below the sand raking machine 4, the other end of the collection belt 6 is connected to one end of the transfer belt 7 through the iron remover 5, and the signal output end of the PLC controller is respectively connected to the upper hopper elevator 1 through the remote IO module. , with a discharge belt 2, a discharge trolley 3, a sand rake machine 4, an iron remover ...
PUM
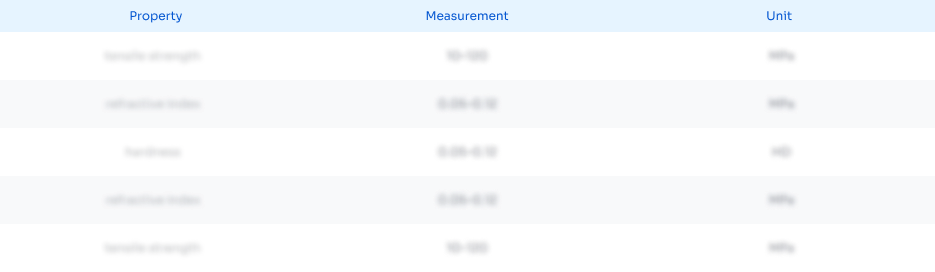
Abstract
Description
Claims
Application Information

- R&D
- Intellectual Property
- Life Sciences
- Materials
- Tech Scout
- Unparalleled Data Quality
- Higher Quality Content
- 60% Fewer Hallucinations
Browse by: Latest US Patents, China's latest patents, Technical Efficacy Thesaurus, Application Domain, Technology Topic, Popular Technical Reports.
© 2025 PatSnap. All rights reserved.Legal|Privacy policy|Modern Slavery Act Transparency Statement|Sitemap|About US| Contact US: help@patsnap.com