DCS (distributed control system) control method and SMITH controller
A control method and controller technology, applied in the direction of adaptive control, comprehensive factory control, comprehensive factory control, etc., can solve problems such as poor effect, no pure delay link, and unrealizable SMITH control structure, so as to eliminate lag problems and improve The effect of stability
- Summary
- Abstract
- Description
- Claims
- Application Information
AI Technical Summary
Problems solved by technology
Method used
Image
Examples
Embodiment Construction
[0023] The present invention will be described in detail below in conjunction with the accompanying drawings.
[0024] The SMITH controller of DCS control of the present invention, as Figure 4 As shown, it includes the adjusted actual value module 6, No. 1 subtraction module 7, No. 2 subtraction module 8, PID controller 2, actuator M / A station 10, actuator output module 11, process quantity module 12, setting Value module 17, proportional coefficient trimming function device 13, multiplier 14, No. 3 subtraction module 15, multi-order inertia time constant function device 16, pure delay time function device 18, No. 1 first-order inertia link 19, No. 2 first-order inertia Link 20, No. 3 first-order inertial link 21, No. 4 first-order inertial link 22, No. 5 first-order inertial link 23, and No. 6 first-order inertial link 9. The adjusted actual value module and the set value module are electrically connected to the No. 1 subtractor, and the No. 1 subtraction module, the No. 2 ...
PUM
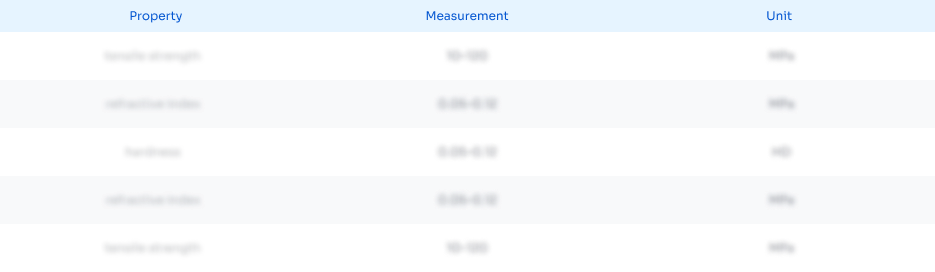
Abstract
Description
Claims
Application Information

- Generate Ideas
- Intellectual Property
- Life Sciences
- Materials
- Tech Scout
- Unparalleled Data Quality
- Higher Quality Content
- 60% Fewer Hallucinations
Browse by: Latest US Patents, China's latest patents, Technical Efficacy Thesaurus, Application Domain, Technology Topic, Popular Technical Reports.
© 2025 PatSnap. All rights reserved.Legal|Privacy policy|Modern Slavery Act Transparency Statement|Sitemap|About US| Contact US: help@patsnap.com