Preparation method for superamphiphobic surface of aluminum and alloy thereof
A technology of super-amphiphobic surface and aluminum alloy sheet, which is applied in metal material coating process, liquid chemical plating, coating, etc. It can solve the problems of inability to realize large-area preparation, large anodic oxidation current, and harsh process conditions. Achieve the effects of environmental protection, good antifouling performance and drag reduction performance, and simple preparation method
- Summary
- Abstract
- Description
- Claims
- Application Information
AI Technical Summary
Problems solved by technology
Method used
Examples
Embodiment 1
[0030] Use 800-grit sandpaper to evenly polish a 6cm×2cm rectangular aluminum sheet, and then use 1700-grit sandpaper to evenly polish it. Ultrasonic cleaning with acetone and ethanol solutions for 10 minutes respectively, and cleaning with deionized water, electrochemically etching the treated aluminum sheet in 0.08M NaCl solution, using graphite or aluminum sheet as cathode, DC voltage 10V, temperature to room temperature and reacted for 2 hours. After the aluminum sheet was taken out, it was ultrasonically cleaned in deionized water for 5 minutes to remove the aluminum oxide particles attached to the surface.
[0031] Then put the aluminum or aluminum alloy sheet at an angle of 60° into a sealed bottle filled with a mixed solution of zinc nitrate (zinc nitrate hexahydrate) and hexamethylenetetramine at a concentration of 0.05M, 50mL, and keep the water at a constant temperature of 90°C. Thermal synthesis, take out the aluminum or aluminum alloy sheet after 3 hours, replace...
Embodiment 2
[0034] A 6cm×2cm rectangular aluminum sheet was evenly sanded with 800-grit sandpaper, and then evenly sanded with 1700-grit sandpaper. Ultrasonic cleaning with acetone and ethanol solutions for 10 minutes respectively, and cleaning with deionized water, the processed aluminum sheet was cleaned in 0.02M Na 2 SO 4 Electrochemical etching in solution, using graphite or aluminum plate as cathode, direct voltage 8V, temperature at room temperature, and reacting for 2.5 hours. After the aluminum sheet was taken out, it was ultrasonically cleaned in deionized water for 5 minutes to remove the aluminum oxide particles attached to the surface.
[0035]Then put the aluminum or aluminum alloy sheet at an angle of 70° into a sealed bottle filled with a mixed solution of zinc nitrate (zinc nitrate hexahydrate) and hexatetramine with a concentration of 0.025M and 50mL. Thermal synthesis, take out the aluminum or aluminum alloy sheet after 3 hours, replace the reaction solution, put the a...
Embodiment 3
[0038] Use 800-grit sandpaper to evenly polish a 6cm×2cm rectangular aluminum sheet, and then use 1700-grit sandpaper to evenly polish it. Ultrasonic cleaning with acetone and ethanol solutions for 10 minutes respectively, and cleaning with deionized water, electrochemically etching the treated aluminum sheet in 0.15M NaCl solution, using graphite or aluminum sheet as cathode, DC voltage 5V, temperature to room temperature and reacted for 3 hours. After the aluminum sheet was taken out, it was ultrasonically cleaned in deionized water for 5 minutes to remove the aluminum oxide particles attached to the surface.
[0039] Then put the aluminum or aluminum alloy sheet into a sealed bottle containing a mixed solution of zinc nitrate (zinc nitrate hexahydrate) and hexamethylenetetramine with a concentration of 0.02M and 50mL at an angle of 60-70°, and keep the temperature at 90°C. ℃ hydrothermal synthesis, take out the aluminum or aluminum alloy sheet after 3 hours, replace the re...
PUM
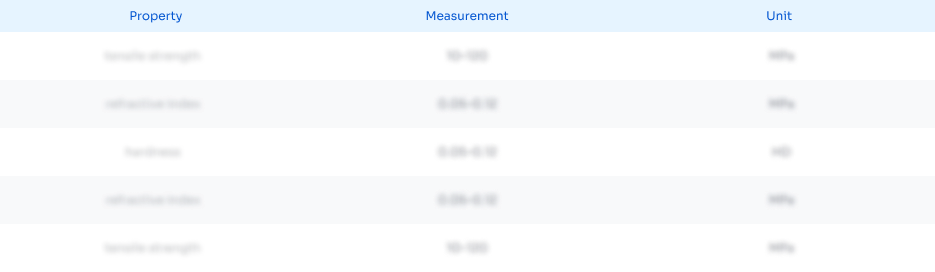
Abstract
Description
Claims
Application Information

- Generate Ideas
- Intellectual Property
- Life Sciences
- Materials
- Tech Scout
- Unparalleled Data Quality
- Higher Quality Content
- 60% Fewer Hallucinations
Browse by: Latest US Patents, China's latest patents, Technical Efficacy Thesaurus, Application Domain, Technology Topic, Popular Technical Reports.
© 2025 PatSnap. All rights reserved.Legal|Privacy policy|Modern Slavery Act Transparency Statement|Sitemap|About US| Contact US: help@patsnap.com