Double-layer V-shaped built-in permanent magnet motor rotor for electric automobile
A technology for electric vehicles and permanent magnet motors, which is applied in the direction of electric vehicles, motors, vehicle components, etc., can solve the problems that the air-gap flux density waveform cannot achieve sinusoidal distribution, it is difficult to meet performance requirements, and the reluctance torque is limited. The effect of saliency ratio and field-weakening speed expansion ability, improvement of air-gap magnetic field waveform, and increase of reluctance torque
- Summary
- Abstract
- Description
- Claims
- Application Information
AI Technical Summary
Problems solved by technology
Method used
Image
Examples
Embodiment 1
[0033] figure 2 It is a cross-sectional view of an embodiment of the double-layer V-shaped built-in permanent magnet motor rotor of the present invention. The rotor includes a rotating shaft (not shown in the figure) and a rotor core 3. The inner circumference of the rotor core 3 is evenly spaced in the radial direction. There are inner and outer double-layer permanent magnet slots 2a, 2b, and the permanent magnet slots 2a, 2b are uniformly inlaid with two rectangular strip magnets 1a, 1b, and the magnets 1a, 1b of each layer are two independent and separated magnets. Steel, two magnets form a V shape, forming inner and outer double-layer V-shaped radially magnetized rectangular strip magnets 1a, 1b, which are called double-layer V-shaped built-in permanent magnets (IPM). The permanent magnetic poles are composed of double-layer V-shaped radially magnetized rectangular strip magnets and pole shoes 8, which greatly reduces the centrifugal force caused by the rotor magnets.
...
Embodiment 2
[0037] On the basis of Embodiment 1, this embodiment optimizes the structure of the rotor.
[0038] Optimizing the polar arc angle α1 of the inner V-shaped magnetic steel 1b:
[0039] By adjusting the pole arc angle α1 of the inner V-shaped magnetic steel 1b, according to the 12 poles of the motor, the angle range of the control pole arc angle α1 is: 24°-27.5°, and the others are the same as in Embodiment 1.
[0040] In this embodiment, the rotor of a 60KW motor for an electric bus is still taken as an example. The relationship between the cogging moment Tcog and the rotation angle θ of the motor rotor structure optimized in this embodiment is as follows Figure 6 As shown, the cogging moment Tcog peak value is 13Nm.
[0041] The effect of polar arc angle α1 optimization: combined with Figure 5 , Figure 6 , it can be seen that after the optimization of the polar arc angle α1, the peak value of the cogging moment Tcog is reduced from 16.5Nm before optimization (the unoptim...
Embodiment 3
[0043] On the basis of Embodiment 2, this embodiment further optimizes the structure of the rotor.
[0044] While optimizing the pole arc angle α1 of the inner V-shaped magnetic steel 1b, the included angle α2 between the outer V-shaped magnetic steel 1a is adjusted, and the range of the controlled included angle α2 is: 155°-160°. Others are identical with embodiment 2.
[0045] In this embodiment, the rotor of a 60KW motor for an electric bus is still taken as an example. The relationship between the cogging moment Tcog and the rotation angle θ of the motor rotor structure optimized in this embodiment is as follows Figure 7 As shown, the cogging moment Tcog peak value is 10.85Nm.
[0046] The optimized effect of polar arc angle α1 and included angle α2: combined Figure 5 , Figure 7 , it can be seen that after the optimization of the polar arc angle α1 and the included angle α2, the peak value of the cogging moment Tcog is reduced from 16.5Nm before optimization (initial s...
PUM
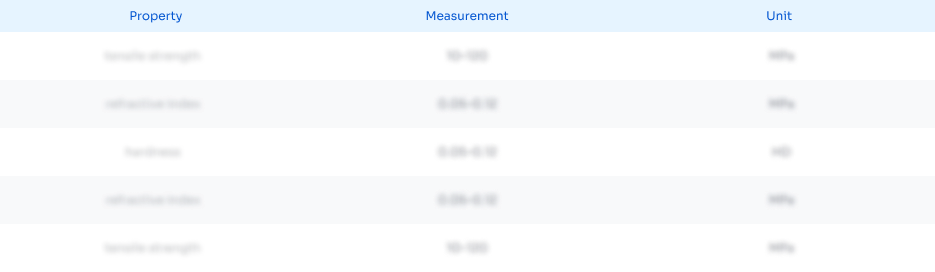
Abstract
Description
Claims
Application Information

- R&D
- Intellectual Property
- Life Sciences
- Materials
- Tech Scout
- Unparalleled Data Quality
- Higher Quality Content
- 60% Fewer Hallucinations
Browse by: Latest US Patents, China's latest patents, Technical Efficacy Thesaurus, Application Domain, Technology Topic, Popular Technical Reports.
© 2025 PatSnap. All rights reserved.Legal|Privacy policy|Modern Slavery Act Transparency Statement|Sitemap|About US| Contact US: help@patsnap.com