Manufacturing method of a screw motor rotor structure
A technology of rotor structure and manufacturing method, which is applied in the manufacture of motor generators, stator/rotor bodies, electromechanical devices, etc., can solve the problems of poor dynamic response performance and large inertia, achieve good dynamic performance, weaken harmonic content, The effect of improving dynamic response performance
- Summary
- Abstract
- Description
- Claims
- Application Information
AI Technical Summary
Problems solved by technology
Method used
Image
Examples
Embodiment Construction
[0033] Below in conjunction with accompanying drawing and specific embodiment the present invention is described in further detail:
[0034] Such as figure 1 Shown is the flow chart of making the structure of the screw motor. It can be seen from the figure that a method for making the rotor structure of the screw motor includes the following steps:
[0035] Step (1), on the axial outer wall of the lead screw nut 2, evenly open n grooves along the circumferential direction, n is a positive integer, and n is greater than or equal to 4; then the lead screw nut 2 is fixed and fitted on the lead screw 1 the outer wall;
[0036] Step (2), in step (1), put n convex keys 3 into the n grooves of the screw nut 2; put the large end of the convex key 3 into the groove, and the small end protrudes from the groove , and after the convex key 3 is installed with the groove, keep the upper surface of the large end of the convex key 3 coincident with the outer surface of the lead screw nut 2;...
PUM
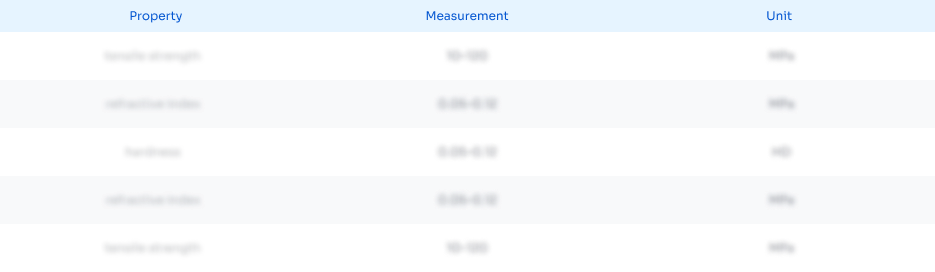
Abstract
Description
Claims
Application Information

- R&D
- Intellectual Property
- Life Sciences
- Materials
- Tech Scout
- Unparalleled Data Quality
- Higher Quality Content
- 60% Fewer Hallucinations
Browse by: Latest US Patents, China's latest patents, Technical Efficacy Thesaurus, Application Domain, Technology Topic, Popular Technical Reports.
© 2025 PatSnap. All rights reserved.Legal|Privacy policy|Modern Slavery Act Transparency Statement|Sitemap|About US| Contact US: help@patsnap.com