Mechanism for Measuring the Rotational Speed of Stable Platform in Dynamic Pointing Rotary Steerable Drilling Tool
A rotary steerable drilling and stable platform technology, applied in the field of oil and gas drilling, can solve the problems of cumbersome signal processing, low measurement accuracy, and complex structure of measurement tools, and achieve the effects of compact structure, precise control, and convenient debugging
- Summary
- Abstract
- Description
- Claims
- Application Information
AI Technical Summary
Problems solved by technology
Method used
Image
Examples
Embodiment 1
[0026] Embodiment 1: as figure 1 As shown, a rotational speed measurement mechanism of a stable platform in a dynamic pointing rotary steerable drilling tool includes a rotating outer cylinder 6 and a stable platform body 1 set in the rotating outer cylinder 6, and the inner side of the rotating outer cylinder 6 is connected with a motor installation Plate 7, a motor 8 is installed in the center of the motor mounting plate 7, the lower end of the motor 8 is transitionally matched with the stable platform body 1 through the coupling 5, and drives the stable platform body 1 to rotate; the upper end of the stable platform body 1 is installed The bearing sleeve 12 inside the rotating outer cylinder 6 and the double-row angular contact ball bearing 2 embedded in the bearing sleeve 12 are connected with the rotating outer cylinder 6, and the outer side of the upper end of the stable platform body 1 is sleeved with a fastening nut 9, The middle part of the fastening nut 9 is provided...
Embodiment 2
[0042] Embodiment 2: Different from Embodiment 1, in Embodiment 2, three magnetic steels are embedded in the lower side of the protruding circular plate in the middle of the fastening nut 9; The interval angle distribution; the Hall sensor circuit board 3 is provided with a single-chip microcomputer 15, an AND gate 14 and six groups of Hall element circuits containing the Hall sensor 4, and the Hall sensors 4 in the six groups of Hall element circuits are evenly distributed on the On the Hall sensor circuit board 3 , each group of Hall element circuits is connected to the single-chip microcomputer 15 through the AND gate 14 .
Embodiment 3
[0043] Embodiment 3: Different from Embodiment 1, in Embodiment 3, four magnetic steels are embedded in the lower side of the protruding circular plate in the middle of the fastening nut 9; The interval angle distribution; the Hall sensor circuit board 3 is provided with a single chip microcomputer 15, an AND gate 14 and six groups of Hall element circuits containing the Hall sensor 4, and the Hall sensors 4 in the six groups of Hall element circuits are evenly distributed On the Hall sensor circuit board 3 , each group of Hall element circuits is connected to the single-chip microcomputer through an AND gate.
PUM
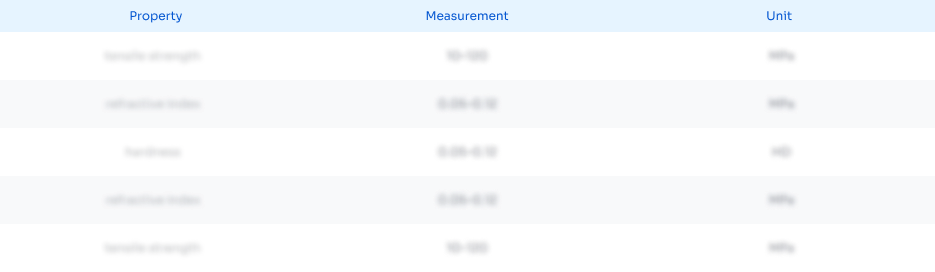
Abstract
Description
Claims
Application Information

- R&D
- Intellectual Property
- Life Sciences
- Materials
- Tech Scout
- Unparalleled Data Quality
- Higher Quality Content
- 60% Fewer Hallucinations
Browse by: Latest US Patents, China's latest patents, Technical Efficacy Thesaurus, Application Domain, Technology Topic, Popular Technical Reports.
© 2025 PatSnap. All rights reserved.Legal|Privacy policy|Modern Slavery Act Transparency Statement|Sitemap|About US| Contact US: help@patsnap.com