Workpiece positioning method in robot transportation system by means of intelligent camera
A technology of smart camera and handling system, applied in manipulators, manufacturing tools, etc., can solve the problems of high labor intensity, can not be widely used, high risk, etc., to reduce the labor intensity of personnel, shorten the production cycle, and achieve a high degree of automation. Effect
- Summary
- Abstract
- Description
- Claims
- Application Information
AI Technical Summary
Problems solved by technology
Method used
Image
Examples
Embodiment Construction
[0033] The technical scheme of the present invention will be further described below in conjunction with the accompanying drawings and through specific embodiments:
[0034] Aiming at the problems existing in the prior art, the object of the present invention is to provide a method for locating a workpiece in a robot handling system using a smart camera, which uses a combination of a smart camera 4 and a robot for automatic positioning and handling, with high degree of automation, high efficiency and It has high precision and can be applied to the needs of high-volume high-precision stamping production.
[0035] see Figure 1 to Figure 4 , the present invention provides a method for positioning a workpiece using a smart camera in a robot handling system, wherein the robot handling system includes a handling robot 1, a positioning platform 2, a push rod 3, a smart camera 4 and an LED light source 5, the The positioning platform 2 is located within the operating range of the ha...
PUM
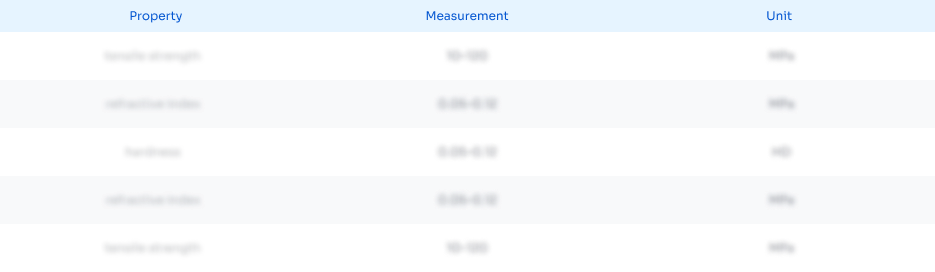
Abstract
Description
Claims
Application Information

- R&D
- Intellectual Property
- Life Sciences
- Materials
- Tech Scout
- Unparalleled Data Quality
- Higher Quality Content
- 60% Fewer Hallucinations
Browse by: Latest US Patents, China's latest patents, Technical Efficacy Thesaurus, Application Domain, Technology Topic, Popular Technical Reports.
© 2025 PatSnap. All rights reserved.Legal|Privacy policy|Modern Slavery Act Transparency Statement|Sitemap|About US| Contact US: help@patsnap.com