High-purity hollow silicon material, as well as polycrystalline silicon and ingot silicon vacuum solid-liquid separation method and equipment
A solid-liquid separation, polysilicon technology, applied in the direction of polycrystalline material growth, chemical instruments and methods, crystal growth, etc., can solve problems such as low yield, and achieve the effects of reasonable equipment structure, inhibition of reverse diffusion, and simple operation.
- Summary
- Abstract
- Description
- Claims
- Application Information
AI Technical Summary
Problems solved by technology
Method used
Image
Examples
Embodiment 1
[0038] This embodiment discloses a device capable of realizing the vacuum solid-liquid separation method of polycrystalline silicon ingot silicon, such as figure 1 As shown, the equipment includes a quartz crucible 4, a pressure rod 1, a vacuum device, a cooperating furnace cover 2 and a furnace body 3; after the furnace cover 2 and the furnace body 3 cooperate, a sealed operating system can be formed. The pipeline 15 communicates with the vacuuming equipment, and the vacuuming equipment is a mechanical pump 13 and a Roots pump 14 connected in series; the lower end of the furnace body 3 is provided with an ingot pulling device, and the quartz crucible 4 is fixed on the ingot pulling device near the inner side of the furnace body 3, The outside of the quartz crucible 4 is fixed with an induction coil 7 ; Moving the pressing rod 1 can realize the movement of the pressing rod 1 relative to the material in the quartz crucible 4 .
[0039] The outside of the quartz crucible 4 is a...
Embodiment 2
[0047] Using the same equipment as in Example 1 to carry out polysilicon ingot silicon vacuum solid-liquid separation, comprising the following steps:
[0048] The first step: smelting and pulling the ingot
[0049] In the quartz crucible 4, the silicon material that accounts for 93% of the volume of the quartz crucible is loaded, and the purity of the silicon material is 99.7%. Close the furnace cover 2 so that the inside of the furnace body 3 is in a sealed state, and utilize the mechanical pump 13 and the Roots pump 14 to move the furnace body 3 The interior is evacuated to 3Pa, the induction coil 7 is heated, the temperature inside the quartz crucible 4 is kept at 1000°C by means of a temperature control couple, and the furnace body 3 is filled with 6×10 helium gas with a purity of 99.9%. 4 Pa, again use the mechanical pump 13 and Roots pump 14 to vacuumize to 3Pa, and fill the furnace body 3 with helium 6×10 4 Pa, use the induction coil 7 to raise the temperature in th...
Embodiment 3
[0054] Using the same equipment as in Example 1 to carry out polysilicon ingot silicon vacuum solid-liquid separation, comprising the following steps:
[0055] The first step: smelting and pulling the ingot
[0056] In the quartz crucible 4, the silicon material that accounts for 95% of the volume of the quartz crucible is loaded, and the purity of the silicon material is 99.9%. Close the furnace cover 2 so that the inside of the furnace body 3 is in a sealed state, and utilize the mechanical pump 13 and the Roots pump 14 to move the furnace body 3. Vacuumize the interior to 7Pa, heat the induction coil 7, use the temperature control couple to keep the temperature in the quartz crucible 4 at 1200°C, and fill the furnace body 3 with argon gas 8×10 4 Pa, again use the mechanical pump 13 and Roots pump 14 to vacuumize to 7Pa, and fill the furnace body 3 with argon gas 8×10 4 Pa, use the induction coil 7 to raise the temperature in the quartz crucible 4 to 1650 ° C, and the mol...
PUM
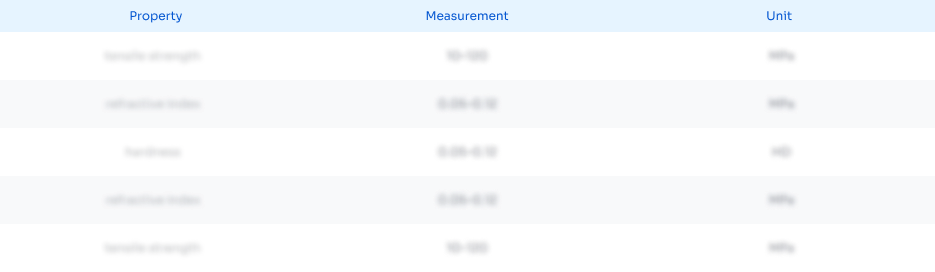
Abstract
Description
Claims
Application Information

- Generate Ideas
- Intellectual Property
- Life Sciences
- Materials
- Tech Scout
- Unparalleled Data Quality
- Higher Quality Content
- 60% Fewer Hallucinations
Browse by: Latest US Patents, China's latest patents, Technical Efficacy Thesaurus, Application Domain, Technology Topic, Popular Technical Reports.
© 2025 PatSnap. All rights reserved.Legal|Privacy policy|Modern Slavery Act Transparency Statement|Sitemap|About US| Contact US: help@patsnap.com