Recycle of calcium phosphate
A technology of phosphorous acid and sodium hypophosphite, applied in phosphorous acid, phosphorus oxyacid and other directions, can solve the problems of high energy consumption, complex operation process, high process condition requirements, etc., and achieve low energy consumption, simple process and product purity. high effect
- Summary
- Abstract
- Description
- Claims
- Application Information
AI Technical Summary
Problems solved by technology
Method used
Image
Examples
Embodiment 1
[0012] Take 400g of solid precipitate containing 48% calcium phosphite from the plate and frame filter press in the sodium hypophosphite production workshop, wash away the sodium hypophosphite in it with water, put it into a 2L flask with stirring, add 1000ml of water, heat and stir , add 180g of soda ash, raise the temperature of the feed liquid to 85°C, keep it warm and stir for 10h, and filter out the calcium carbonate precipitate while it is hot. Add 47g of the reclaimed phosphorous acid solution containing 50% phosphorous acid prepared in advance, adjust the pH to 5~6, remove excess soda ash, and pass through H 2 After S removes the heavy metal, obtain 1530g of 13.6% sodium phosphite solution, wherein H 2 S is generated by the reaction of sodium sulfide and phosphoric acid in the hydrogen sulfide reactor, and the excess H in the filtrate 2 S is recycled through the aeration tower.
[0013] On the cation exchange column equipped with D001 resin, the obtained sodium phosp...
Embodiment 2
[0015] Take 400g of solid precipitate containing 50% calcium phosphite from the plate and frame filter press in the sodium hypophosphite production workshop, wash off the sodium hypophosphite in it with water, put it into a 2L flask equipped with stirring, add 1000ml of water, heat and stir , add 185g of soda ash, raise the temperature of the feed solution to 90°C, keep stirring and react for 10h, and filter out the calcium carbonate precipitate while it is hot. Add 47g of the recovered phosphorous acid liquid containing 50% phosphorous acid prepared in advance, adjust the pH to 5~6, remove excess soda ash, and pass through H 2 After S removes the heavy metal, obtain 1535g of 14% sodium phosphite solution, wherein H 2 S is generated by the reaction of sodium sulfide and phosphoric acid in the hydrogen sulfide reactor, and the excess H in the filtrate 2 S is recycled through the aeration tower.
[0016] On the cation exchange column equipped with D001 resin, the obtained sodi...
Embodiment 3
[0018] Take 400g of solid precipitate containing 52% calcium phosphite from the plate and frame filter press in the sodium hypophosphite production workshop, wash away the sodium hypophosphite in it with water, put it into a 2L flask equipped with stirring, add 1000ml of water, heat and stir , add 180g of soda ash, raise the temperature of the feed solution to 85°C, keep it warm and stir to react for 5h, and filter out the calcium carbonate precipitate while it is hot. Add 47g of the recovered phosphorous acid liquid containing 50% phosphorous acid prepared in advance, adjust the pH to 5~6, remove excess soda ash, and pass through H 2 After S removes the heavy metal, obtain 1550g of 13.8% sodium phosphite solution, wherein H 2 S is generated by the reaction of sodium sulfide and phosphoric acid in the hydrogen sulfide reactor, and the excess H in the filtrate 2 S is recycled through the aeration tower.
[0019] On the cation exchange column equipped with D001 resin, the obta...
PUM
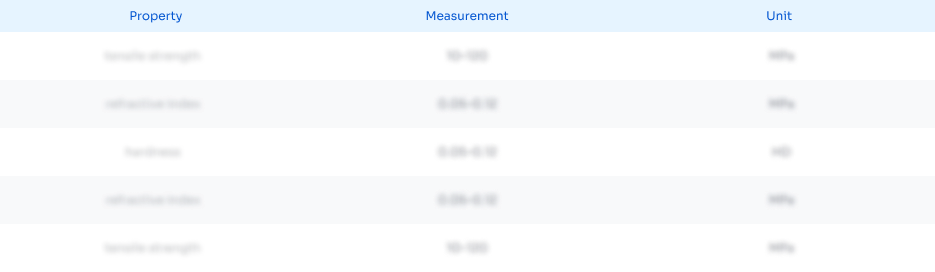
Abstract
Description
Claims
Application Information

- R&D
- Intellectual Property
- Life Sciences
- Materials
- Tech Scout
- Unparalleled Data Quality
- Higher Quality Content
- 60% Fewer Hallucinations
Browse by: Latest US Patents, China's latest patents, Technical Efficacy Thesaurus, Application Domain, Technology Topic, Popular Technical Reports.
© 2025 PatSnap. All rights reserved.Legal|Privacy policy|Modern Slavery Act Transparency Statement|Sitemap|About US| Contact US: help@patsnap.com