Double-end-surface grinding equipment of micro drillstock
A double-end surface grinding technology, which is applied in the direction of grinding/polishing equipment, metal processing equipment, grinding machine tool parts, etc., can solve the problems of large manpower consumption, poor reduction of different diameter welding, material length and rough end surface, etc. problem, to achieve the effect that it is not easy to deviate
- Summary
- Abstract
- Description
- Claims
- Application Information
AI Technical Summary
Problems solved by technology
Method used
Image
Examples
Embodiment 1
[0015] Embodiment 1, a kind of double end surface grinding equipment of micro-drill shank, comprises body 1, is provided with a grinding assembly on body 1, and described grinding assembly is made up of two grinding wheels 3 and the rotation that is arranged in parallel in the middle of two grinding wheels 3 The tooth plate 2 is composed of a grinding assembly with a feeding hopper 5 above and a receiving chute 7 below. Both the loading hopper 5 and the receiving chute 7 are tangent to the rotating tooth plate 2, and the two tangent points There is a pressing belt 4 on the edge of the rotating tooth plate 2 between them, the edge of the rotating tooth plate 2 is provided with a tooth groove 8, the two grinding wheels 3 are connected with the body 1 through the telescopic shaft 9 at the center of the circle, and the grinding machine body 1 is provided with 3 The diameter of the motor 6 and the grinding wheel 3 is greater than or equal to the diameter of the rotary crankset 2. Wh...
PUM
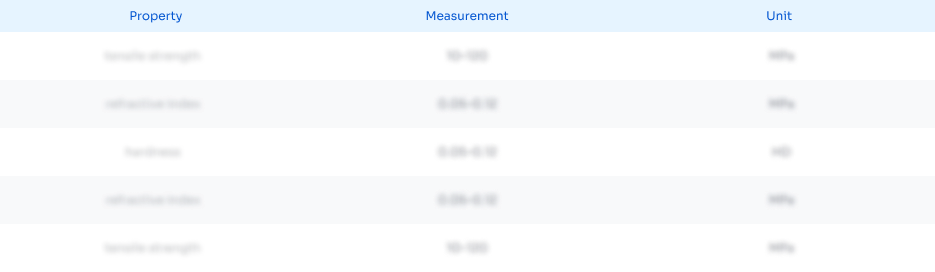
Abstract
Description
Claims
Application Information

- Generate Ideas
- Intellectual Property
- Life Sciences
- Materials
- Tech Scout
- Unparalleled Data Quality
- Higher Quality Content
- 60% Fewer Hallucinations
Browse by: Latest US Patents, China's latest patents, Technical Efficacy Thesaurus, Application Domain, Technology Topic, Popular Technical Reports.
© 2025 PatSnap. All rights reserved.Legal|Privacy policy|Modern Slavery Act Transparency Statement|Sitemap|About US| Contact US: help@patsnap.com